introduction
Cutting speed is a critical factor in machining operations because it directly affects the efficiency and quality of the process. There are many factors that affect cutting speed, and understanding these factors is essential to achieving the best results. Good CNC turned parts manufacturers are better able to avoid these factors.
1.Machining Materials
Different materials have different hardness and characteristics, which directly affects their cutting speed. Harder materials, such as stainless steel or titanium, require lower speeds to prevent excessive tool wear and maintain dimensional accuracy. On the other hand, softer materials, such as aluminum or plastic, can be cut at higher speeds without affecting the quality of the finished product.
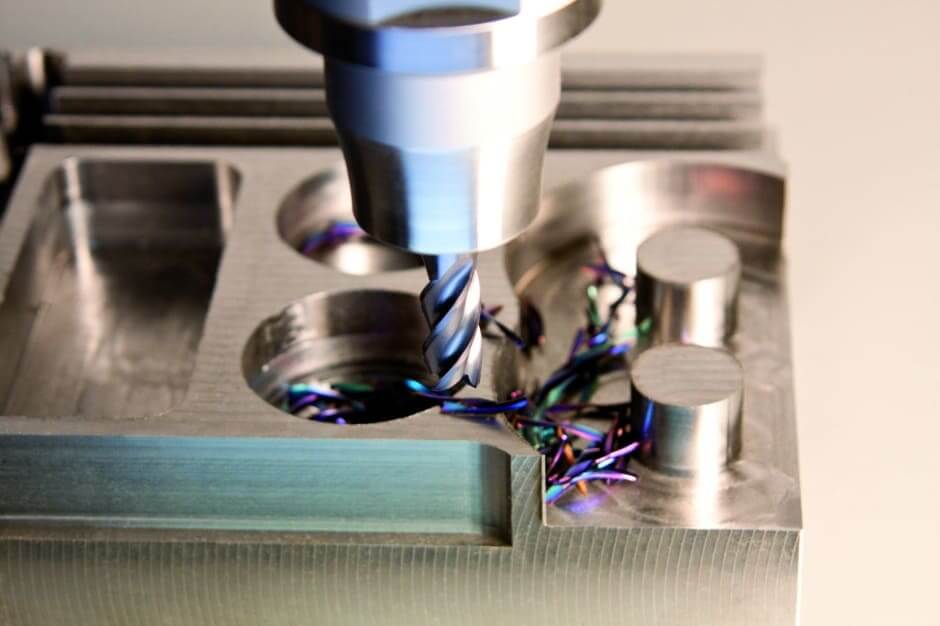
2.Types of Cutting Tools
Since different cutting tools have different capabilities and limitations, this determines the maximum speed at which they can operate effectively. For example, carbide cutting tools are known for their high-speed capabilities and can withstand higher cutting speeds than high-speed steel tools. Therefore, carefully consider the choice of cutting tool material and design to ensure compatibility with the required speed.
3.Depth of Cut
Depth of cut refers to the thickness of material removed in a single cut. Increasing the depth of cut allows for higher cutting speeds, as more material can be removed per revolution of the cutting tool. However, it is critical to strike a balance between depth of cut and cutting speed to avoid excessive tool wear and potential damage to the workpiece.
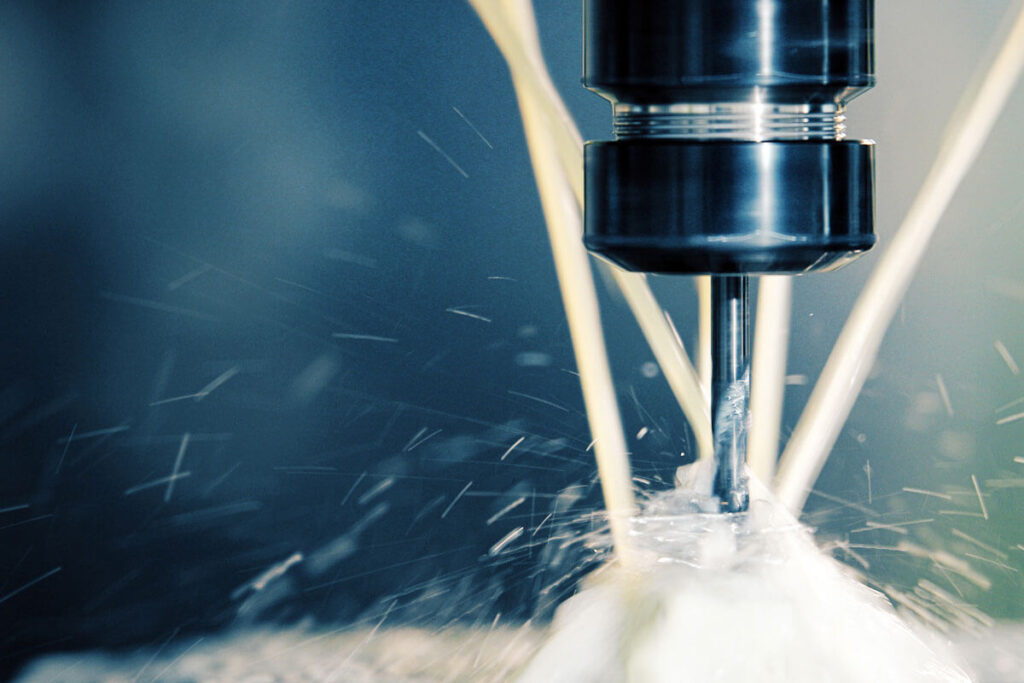
4.Rigidity of Machine Tool and Workpiece Setup
A stable and rigid setup enables higher cutting speeds because it minimizes vibrations and ensures precise cutting. On the other hand, a weak or unstable setup can lead to chatter, poor surface finish and reduced tool life.
5.Cutting Fluids
Cutting fluids have many purposes, including cooling the cutting tool and workpiece, lubricating the cutting zone and flushing away chips. By reducing heat and friction, cutting fluids can increase cutting speeds and extend tool life. Cutting fluid selection should be based on the material being machined and the specific machining operation to optimize speed and overall performance.
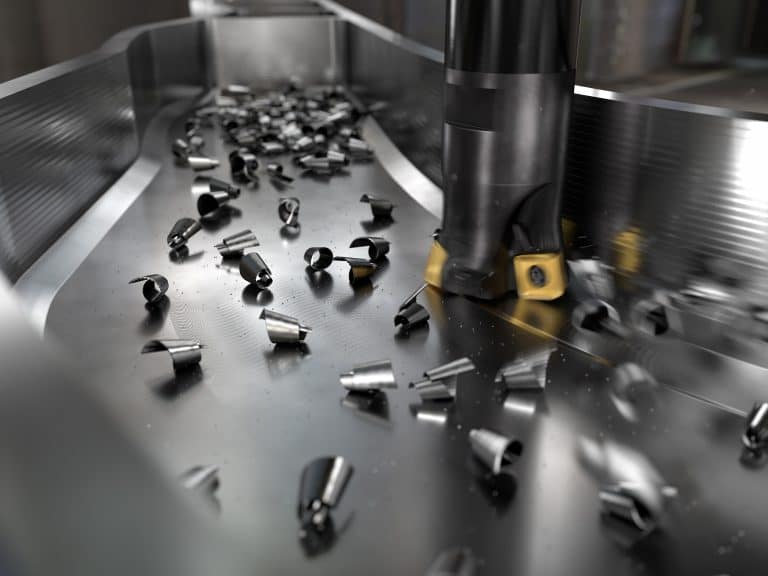
6.Feed Rate
This refers to the speed at which the cutting tool advances along the workpiece. The higher the feed rate, the faster the cutting speed because more material is removed per unit time. However, the limitations of the cutting tool and workpiece material must be considered to avoid excessive tool wear or damage.
7.In summary
Cutting speed is affected by a variety of factors, including the material being machined, the type of cutting tool, the depth of cut, the rigidity of the machine tool setup, the cutting fluid used and the feed rate. Understanding these factors and their interactions is essential to achieving the optimal cutting speed in a machining operation.
By carefully considering these factors and making informed decisions, fabricators and CNC turned part manufacturers can increase productivity, improve surface finish and extend tool life.