We Care Your
Passivation & Electrolytic polishing Solution
Proactively coordinate quality quality vectors vis-a-vis supply chains
quickly engage client-centric comprehensive services.
Our qualifications:
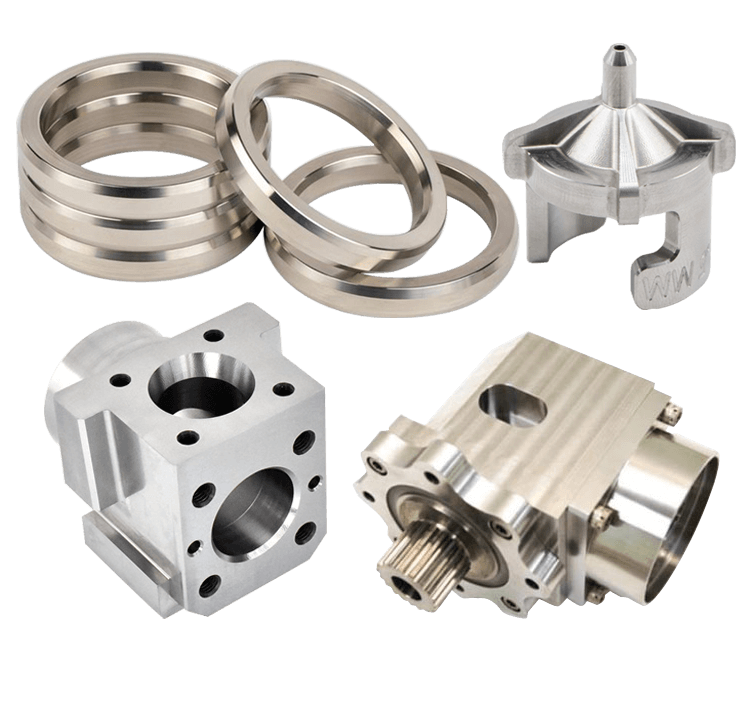
Surface finishes
Passivation & Electrolytic polishing services
Electropolishing and passivation are both effective methods of improving metal corrosion resistance and surface finish. Electropolishing removes a thin layer of metal, leaving a smooth and reflective surface, while passivation creates a protective oxide layer on the surface to improve surface roughness and corrosion resistance.
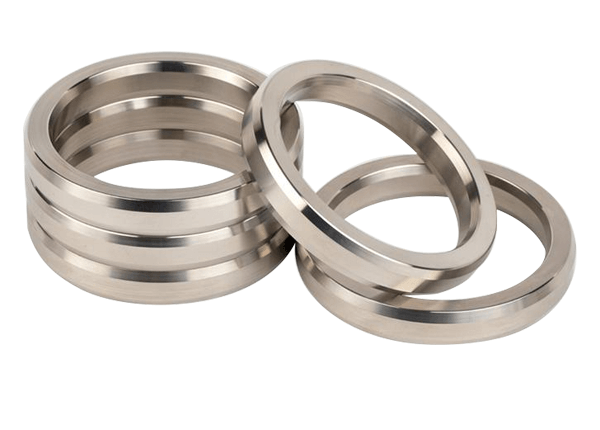
Part surface treatment
Passivation & Electropolishing of CNC Machined Stainless Steel Parts
- Principle of stainless steel passivation Passivation is a method to change the metal surface into a state that is not easy to be oxidized and slow down the corrosion rate of the metal. Metal corrosion products generated as a result of the action of medium if has compact structure, forming a layer of thin film, tightly covered on the surface of metal, change the surface state of metal, the metal electrode potential jump towards is greatly, and become the passivity of the corrosion, and shows the corrosion resistance performance of precious metals, this layer is called passivation film.
- Principle of stainless steel electrolytic polishing Stainless steel electropolishing is mainly aimed at the surface bright treatment of stainless steel workpiece. The workpiece is cast as the anode, insoluble metal as the cathode, both poles are immersed in the electrolytic cell at the same time, through direct current to produce selective anodic dissolution, the workpiece surface gradually leveled, so as to achieve the effect of increasing the surface brightness of the workpiece.
Description of type: (Reference standard: ASTM A967)
- Stainless steel nitric acid passivation type
Types | Solution (volume percentage) | solution temperature(℃) | Minimum immersion time(min) | Xavier |
Nitric 1 | 20% -25% nitric acid and 2.5% + 0.5% of the heavy inscription acid sodium (environmental protection) | 50-55 | 20 | √ |
Nitric 2 | 20%-45% nitric acid | 20-30 | 30 | √ |
Nitric 3 | 20%-25% nitric acid | 50-60 | 20 | √ |
Nitric 4 | 45%-55% nitric acid | 50-55 | 30 | √ |
- Stainless steel citric acid passivation type
Types | Solution (volume percentage) | solution temperature(℃) | Minimum immersion time(min) | Xavier |
Citric 1 | 4%-10%citric acid | 60-71 | 4 | √ |
Citric 2 | 4%-10%citric acid | 49-60 | 10 | √ |
Citric 3 | 4%-10%citric acid | 20-49 | 20 | √ |
Critical items
Non standard requests
* We offer ASTM A967 passivation standards. If you have specific requirements, please contact sales@xavier-parts.com
**Passivation test methods: boiling water test, wet cloth test, temperature test, water immersion test, salt spray test, wet copper sulfate test.
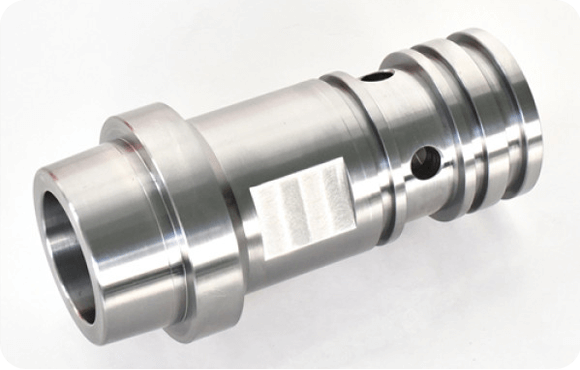
Stainless steel passivation & electrolytic polishing ability
stype | Nitric acid passivation、Citric acid passivation | Electrolyte polishing |
base material | Stainless steel series | 300 series stainless steel |
standard | ASTN A967 | GB/T 20016 |
Maximum machining size(cm) | 100*45*80 | 100*45*80 |
Unit Max Weight(kg) | 80 | 50 |
colour | natural color | gloss white |
test method | Boiling water test, wet cloth test, temperature experiment, the water immersion test, salt spray test, humid copper sulfate test experiment | dimensional gauging,Appearance instrumentation |
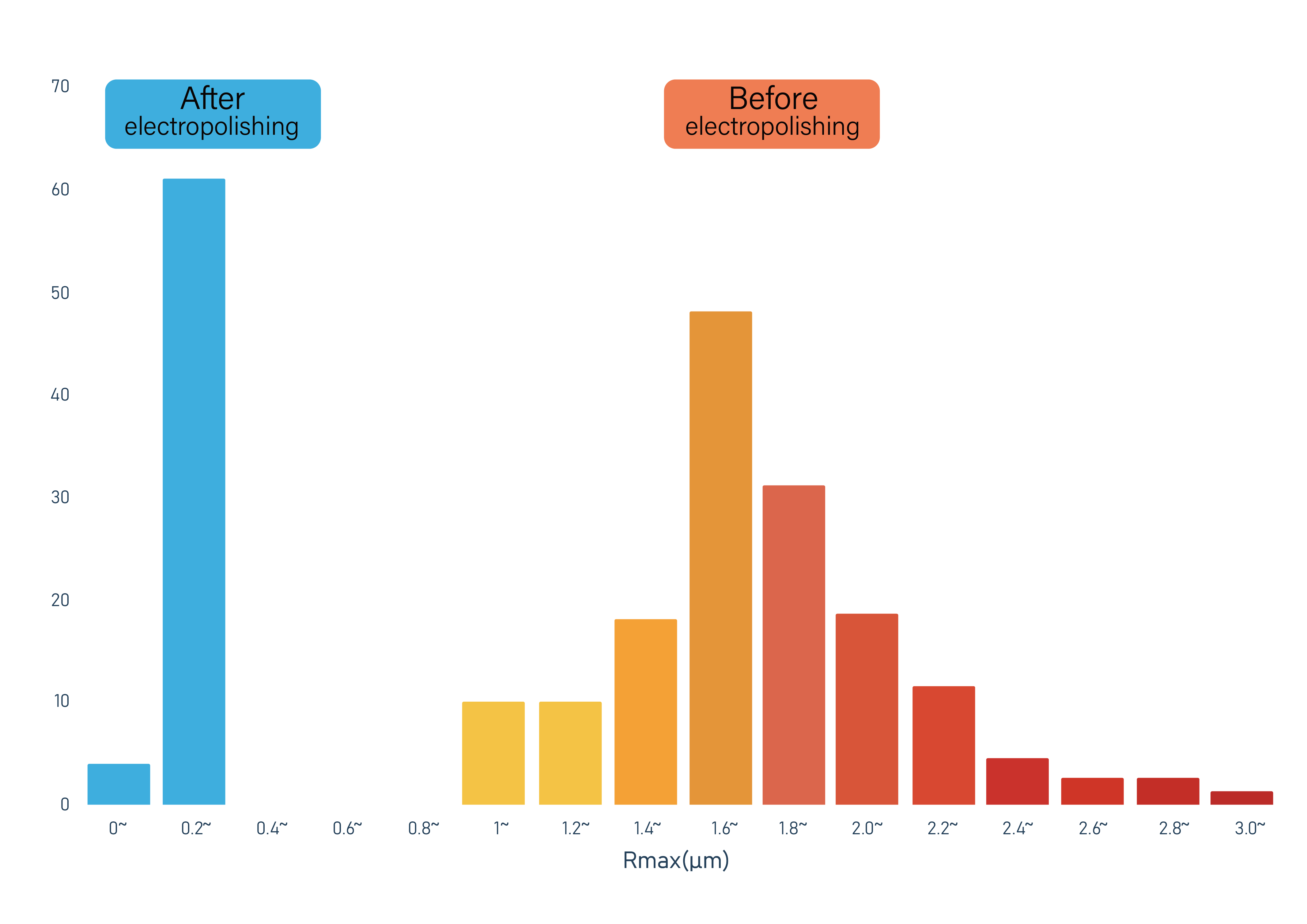
Roughness change of stainless steel electropolishing
Before electropolishing: roughness distribution in 1.0-3.0um. After electropolishing: roughness distribution within 0.3um. The size of electrolytic polishing will only be reduced, and the range of reduction is uncertain. The size of products with better roughness will be thrown off within 10um, and those with larger roughness will be thrown off dozens of um.
Advantage
⑴The color inside and outside is consistent, the luster is long-lasting, and the recesses that cannot be polished by mechanical polishing can be smoothed.
⑵High production efficiency and low cost.
⑶ Increase the corrosion resistance of the workpiece surface.
Quality
We have high standards for Part surface treatment
We manufacture your custom parts according to strict manufacturing standards and ensure all parts and processes adhere to the Xavier Standard. A thorough verification of these requirements is included in our inspection report that we ship with every order.
-
Standard 1
PO consistent
We ensure that every part after machining is as specified in the PO as customer requirements.
-
Standard 2
Quality check
Prior to MP shipment to ensure that each part meets order specifications and Xavier standards.
-
Standard 3
Require consistent
Ensure conformance of parts and any required documentation prior to dispatching the order.