Perfect Quality Service of Die Casting
- Participate in the customer’s previous research and development design (senior project engineer)
- The feasibility of different tests based on the requirements of our customers (mold flow analysis model / 3 d)
- Perfect design team (the senior mold designers)
- Senior production team(fast to solve various problems in production)
Fast Services
Providing reliable solutions from die casting to final finished product.
Free solution
Providing reliable solutions from die casting to final finished product.
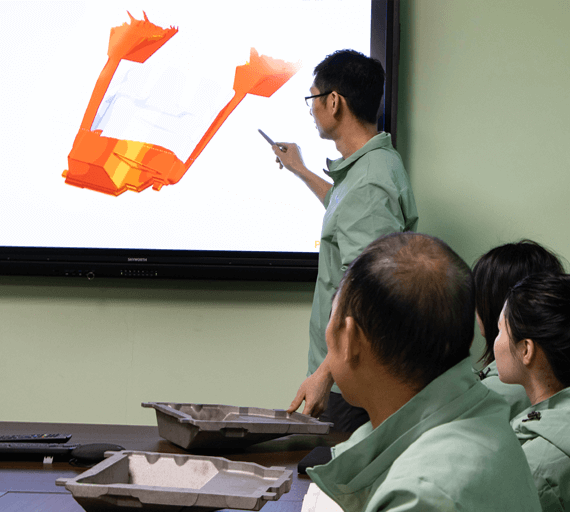
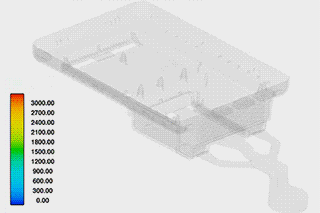