Expanded Metal Mesh Best Practices Guide
1.What is expanded metal mesh?
Expanded metal mesh is a metal mesh made by stretching a cut forgeable metal sheet. The cutting direction is perpendicular to the stretching direction, forming an array of holes formed by the cut sections. Usually a regular pattern of diamond-shaped openings is used. This design can reduce the weight and cost of the sheet while providing ventilation, making it a versatile solution in a variety of applications.
2.Types of expanded metal mesh
(i) Copper mesh
Copper’s corrosion resistance is critical when expanded metal sheets may be exposed to moisture or other reactive environments; copper has better electrical conductivity than most metals available on an industrial scale, and looks good when the mesh is used for decorative purposes. At the same time, copper’s ductility makes it easier to cut and stretch, and can be made into more complex shapes.
(ii) Expanded aluminum
Aluminum is widely used in structural applications due to its high strength and light weight, such as overhead wires. Aluminum’s ductility makes it easier to process than steel in a cold state, and corrosion resistance is also one of its advantages. In addition, aluminum has a high melting point and excellent heat reflectivity, which is very suitable for high temperature environments.
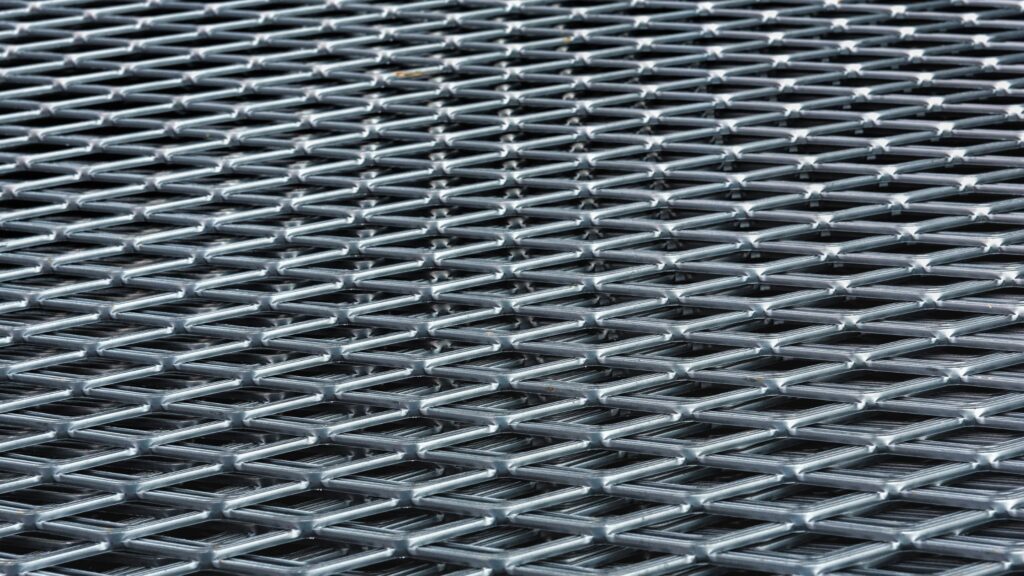
(iii) Steel mesh
Expanded mild steel: provides a strong and economical solution, usually coated with molten zinc through a hot-dip galvanizing process.
Grid metal sheet: Made of higher-gauge metal sheets, usually mild steel.
Stainless steel expanded mesh: Compared with mild steel, stainless steel has stronger corrosion resistance and is more effective in high temperature environments.
3.Manufacturing process of expanded metal mesh
(I) Sheet metal selection
The first step in manufacturing expanded metal is to select the appropriate metal sheet, which depends on the specific purpose of the expanded metal. When selecting metal, you need to consider rigidity, corrosion resistance, strength, appearance, specific gravity, toughness, flexibility, elasticity and other characteristics, and size is also an important consideration.
(II) Metal sheet size
The size of the metal sheet includes the total area covered by the metal sheet before expansion, thickness, flatness and squareness, the size of each cut (that is, the size of each hole), the size of the grid, etc. For diamond grids, the long and short sides of the diamond, the length of the opening and the short opening method, etc. need to be considered. Before expansion, the metal sheet needs to be cut to the required size, usually using an automatic paper cutter, and the required pattern determines the size of the expanded metal sheet.
(III) Cutting and stretching metal
The cutting process forms an opening in the metal mesh and determines its final size. It can be divided into two independent steps of cutting and stretching or a more commonly used single combined operation. Using a die to define a half row across the width of the sheet, the metal sheet is aligned with the inner edge of the die and the support platform, and then the sheet is fed under the die for cutting and stretching at a rate corresponding to the thickness of the wire.
(IV) Opening shape
The opening shapes of expanded metal mesh include diamond, hexagon, square, louvered and decorative. Diamond is the most commonly used pattern, hexagon is achieved by extending the keys of the diamond, square is a variation of diamond, louvered appearance will cause minimal expansion, and decorative opening shape can be customized according to specific aesthetic and architectural needs.
(V) Strand thickness
The wire thickness affects the total percentage of open area in the expanded metal sheet and the ratio of the total area of the expanded sheet to the total area of the original solid sheet. The feed rate during the stretching process affects the wire thickness. The higher the feed rate, the lower the percentage of open space. The feed rate can be adjusted during the production process to achieve different wire thicknesses in a single sheet.
(VI) Flattening process
When a flat surface is required, the flattening process can be performed by cold rolling to make the expanded metal mesh surface flat. Typically, the cutting and stretching process will give the metal a ridged or corrugated texture, called a raised surface. After flattening, the metal mesh will become thinner and elongated in the direction of the roller, causing the opening to stretch in the same direction, which may appear longer or wider than the standard metal mesh.
(VII) Metal flattening
Metal flattening is different from flattening. Flattening deals with surface texture, while metal flattening ensures that the sheet lies flat on a horizontal surface, involving the three-dimensional geometry of the sheet and the degree of alignment of different points in the same plane. If the metal mesh has no waves and bends, it is considered flat, but it is difficult to completely eliminate these defects, so acceptable tolerances need to be established.
4.Surface treatment and shearing of expanded metal mesh
(I) Surface treatment
Painting
Painting is usually a relatively economical method of treating metal mesh and can be used for aesthetic purposes or to provide some corrosion protection. However, it should be noted that for effective corrosion protection, the paint must remain intact, otherwise any small gaps may cause corrosion under the coating. Among the various coating methods, painting is the least expensive, but it also provides relatively little corrosion protection and requires frequent maintenance.
Powder coating
A spray gun is usually used to spray a plastic powder with static electricity, and then the coated plate is heated to make the plastic bond to the metal surface. Powder coatings tend to be more durable than spray painting.
Galvanizing process
During the galvanizing process, the metal mesh is immersed in molten zinc to form a protective zinc coating that helps protect the mesh from corrosion. However, due to the high temperatures involved, this method has limitations on the size of the metal mesh that can be galvanized, and very fine mesh is generally not suitable for galvanizing.
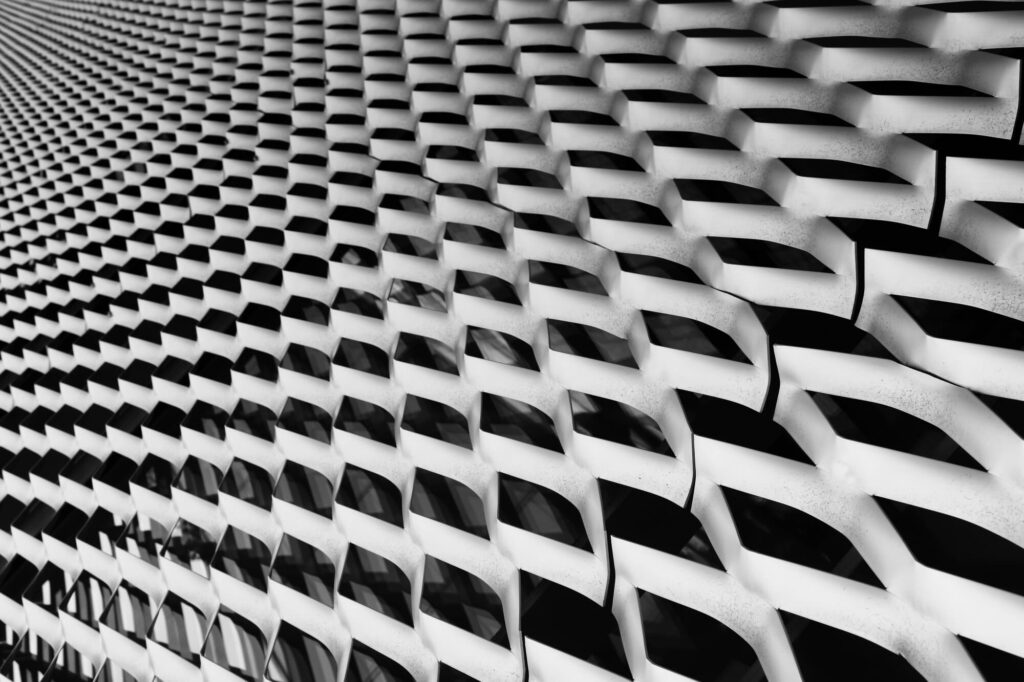
Anodizing process
Anodizing is an electroplating technology that coats expanded metal sheets while they are electrically charged.
It can provide a finer coating and a stronger bond with the metal than other methods. However, due to its high cost, the frequency of use is relatively low.
(II) Metal mesh shearing
Shearing process
Shearing is the process of cutting expanded metal mesh sheets into the required size, which involves trimming larger sheets into smaller parts or changing their shape.
Shearing method
Side shearing: Shearing along the long axis of the diamond pattern.
Key shearing: The sheet is precisely cut along the edge, and a closed shape is formed on both sides of the cut, which is consistent with the shape of the pattern.
Bonding shearing: For raised expanded metal, shearing is performed along the bond between rows.
Random shearing: It does not follow the shape edge, the edge shape is open and the pattern is irregular, which will leave sharp spikes and can be made into a U-shaped edge or frame to improve operability.
Centerline shearing: Shearing along the symmetry line on the expanded metal sheet.
Balance shearing: Create matching parts to ensure that the mesh pattern is continuous.
End shearing: Shearing along the short axis of the diamond.
5.Factors that determine the quality of expanded metal mesh
(i) Tolerance requirements
Tolerances on sheet thickness, strand width, opening size, coating thickness, etc. must be strictly adhered to.
Defects that should not be contained
(ii) Camper curve
Refers to the bow or bend of the sheet. It may not matter if used for packaging, but for applications that require flatter materials, especially those that require higher stiffness, it may cause residual stress in the structure.
(iii) Square properties
Has the properties of a rectangle or square, characterized by 90° angles and straight edges, with equal diagonals. Squareness is a planar property that applies to the top view of the sheet when it is lying flat. Expanded sheets can be square, but they do not need to meet all spatial and geometric requirements.
(iv) Parallel sides
This feature is often critical, especially when the expanded metal sheet has parallel opposite sides. A completely square sheet always has parallel sides, but a sheet with parallel sides is not necessarily square. A sheet without parallel sides is never a square, and parallelism deviations may be caused by factors such as campers.
(V) Cone
Refers to the deviation of the edge from parallelism, which is particularly obvious when the edge is not parallel. Plates with tapered edges cannot be considered square.
(VI) Customized steel plate mesh
Modification based on specific customer requirements, such as cutting to fit specific sizes and frame shapes, creating tears or cuts without separating the original metal sheet fragments, bending plates, connecting sheets, rolling to specific curvatures, etc.
6. Application of Expanded Metal
(1) Metal Platform
Expanded metal mesh is often used in aerial work platforms to take advantage of its light weight. It is also commonly used in rigging in the transportation, petroleum, telecommunications and other industries.
(2) Machine Guards
It can cover rotating shafts and mechanical parts. It is lighter than solid guards and can effectively protect machine operators.
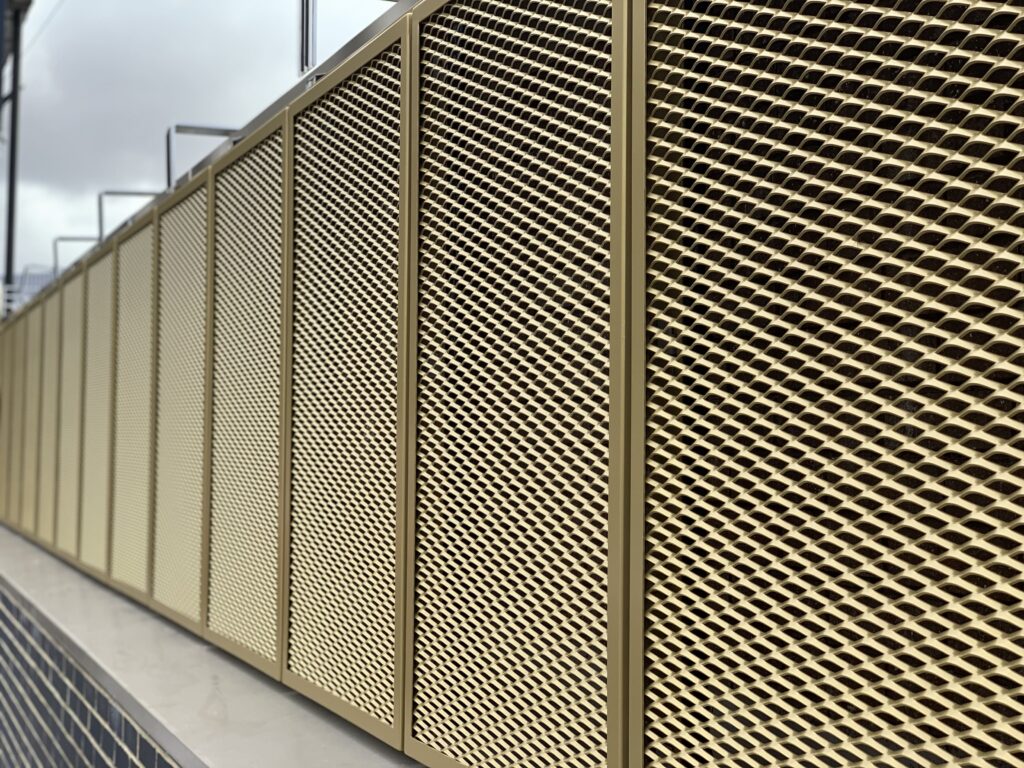
(3) Drainage and Ventilation
It is used for drainage and ventilation of buildings. It is commonly found in drainage ditches in areas such as roadsides, sidewalks, and factory workshops.
(4) Protective Screens
It can be used as a protective screen for windows of buildings and vehicles (including armored vehicles).
(5) Sidewalk Applications
Expanded metal mesh is used in pedestrian areas of some bridges and suspended sidewalks to reduce the weight of the bridge deck while maintaining structural integrity.
(6) Barrier Applications
It is suitable for forming barriers where light, air and water need to pass through. It can be used in structures such as aquariums, buildings, and tunnels.
(7) Fence Applications
It is used for protective fences, yard boundaries, animal cages, etc.
(8) Gabion Walls
It is suitable for making gabion walls and can replace welded mesh when using finer aggregates.
(9)Equipment ventilation
It can be used as equipment cover to provide suitable solutions for equipment such as generators and tractor engines.
(10)Decorative use
It can be used in gardens, building openings, walls, etc. in construction. Fine mesh can also be used for jewelry making.
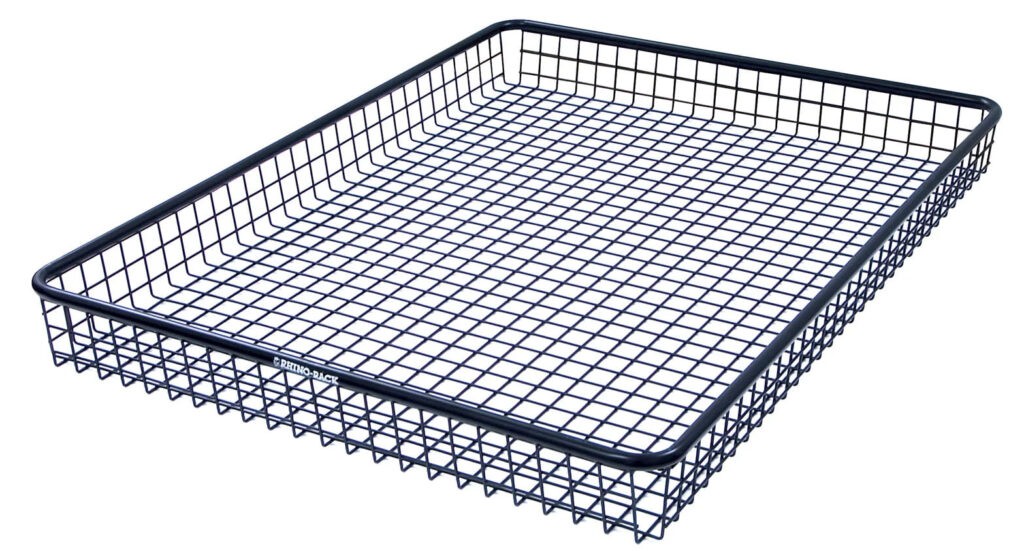
(11)Metal mesh trays
It can be made into agricultural trays for picking and transporting green tea, etc.
(12)Recreational use
Some recreational parks use expansion nets on steep cliffs to provide excitement and entertainment.
7. Advantages of expanded metal
(1) Lightweight advantage
Compared with solid plates of the same size and material, it is relatively light. Expanded metal mesh is thin and light, like flattened metal.
(2) Decorative characteristics
It is decorative and can be used for architectural decoration and jewelry making, etc.
(3) Ventilation and light transmission performance
Allows light and ventilation, and can adjust the amount of light by changing the thickness of the light. Air and light can flow freely, and liquids, dirt, grease and other substances can also pass freely.
(4) Efficient production and zero waste
The output is three times the size of the original solid metal plate, and the manufacturing process does not produce any metal waste, saving metal and the manufacturing process is efficient.
(5) Easy processing
Made from a piece of metal, no connecting materials are required, and it is easier to cut (shear) than solid metal plates.
(6) Recyclability
It has the characteristics of recyclability and meets environmental protection requirements.
(7) Indoor and outdoor applicability
Expanded metal sheets can be used for indoor and outdoor applications, increasing the versatility of the product.
(8) Reinforcement effect
Can be mixed with materials such as glass and concrete to increase strength.
(9) High tensile strength
Can bear more weight and withstand pressure better than woven or welded metal.
(10) Improved sound quality and soundproofing
Can be used for microphones, speakers, and as an extra layer in soundproof rooms and walls.
(11) Low maintenance cost
Maintenance is simple and straightforward, and usually comes with a protective coating to prevent rust.
Summary
As an innovative industrial material, expanded metal mesh has many advantages and a wide range of applications. Its manufacturing process is unique and can be customized according to different needs. In the future, with the continuous development of industry, the demand for expanded metal mesh will continue to grow, providing efficient and reliable solutions for various industries. When selecting and using expanded metal mesh, it is necessary to consider its material type, advantages, applications, etc., in order to give full play to its advantages and meet the needs of practical applications.