Vacuum Casting: Process, Advantages, Disadvantages, and Applications
Vacuum casting is an adaptable manufacturing process that product designers can use to produce small quantities of high-quality prototypes and final products. With relatively low production costs and fine detail, vacuum casting is a powerful tool for rapid prototyping projects and marketing purposes. However, understanding how polyurethane/vacuum casting works will help you achieve the best results.
This article explains the vacuum casting process, how it works, and its advantages and limitations. By reading this article, you will also understand the applications of castings and vacuum casting technical specifications.
1. What is vacuum casting?
Vacuum casting is the same as polyurethane or urethane casting. It is a process that uses a vacuum to draw liquid resin into a mold to create plastic or rubber parts. The vacuum expels air bubbles from the mold to ensure that the casting achieves the desired shape. Rubber, resin, and thermoplastics are liquid materials commonly used in polyurethane casting.
Manufacturers use this process to produce small batches of plastic or metal parts with quality and precise dimensions using a master pattern. However, vacuum cast parts may fail in high heat or pressure applications.
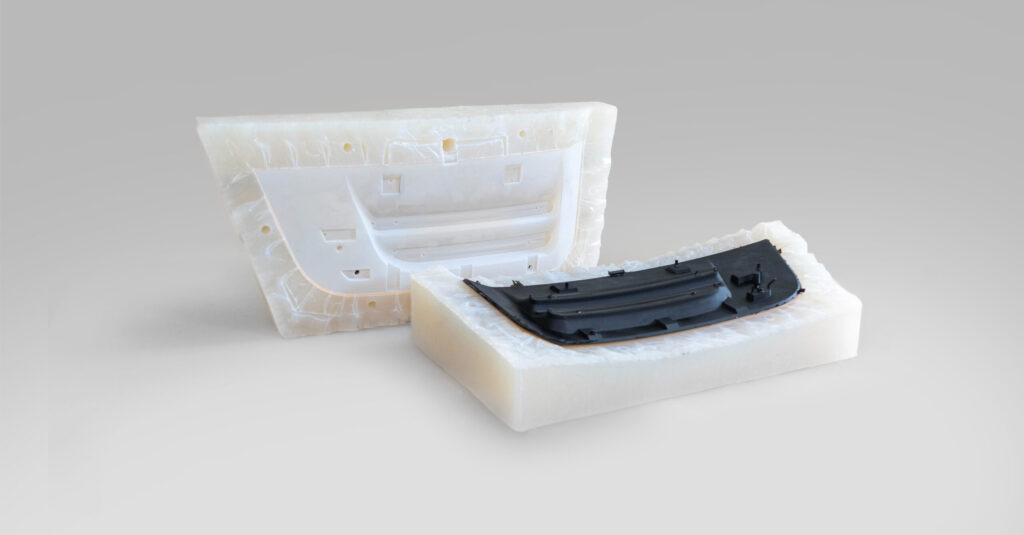
2. How is vacuum casting performed?
Vacuum casting is a modern and technical manufacturing process. It requires a mold that is the same shape as the finished product and uses silicone as the mold instead of metal. Here is a step-by-step guide to how vacuum casting works:
Step 1: Create a 3D Model
The process starts with making a 3D model of the target component. Before creating a 3D model, you must make appropriate calculations to prevent deformation or defects that may affect the finished product after casting.
Therefore, it is crucial to strictly adhere to the principles of injection molding and make appropriate adjustments to the calculations when necessary. CATIA, AutoCAD or Solidworks are typical design software that can be used to develop 3D models for injection molding projects.
Step 2: Create a Master Pattern
Here, you must generate a high-quality master model using the 3D model you created. While manufacturers used to rely on CNC machining to make them, 3D printing technology has made the role of markers more practical and economical. However, the accuracy of CNC machining is better than 3D printing. For high-precision requirements, our customers usually choose CNC machining.
The mold master is a prototype that product designers use to develop silicone molds. The casting pattern is a replica of the master mold. Therefore, any deformation on the master mold will affect the silicone mold. Therefore, it is crucial to prepare the master mold with the utmost precision.
Step 3: Making the Silicone Rubber Mold
Once the master mold is developed, you are ready to cast the silicone mold. These molds are created using the master mold and a casting box. The master mold with its casting cores and inserts inside is suspended in the casting box. Casting sprues and risers are placed in the casting box along with the cores to pour the molten silicone and remove the finished mold.
Hot liquid silicone is poured into the casting box around the master mold and as it flows inside the master mold, it fills all the gaps of the prototype mold. The liquid silicone cures at 40ºC inside the casting box for 8-16 hours. However, the time may vary depending on the size of the silicone mold. The risers are removed and the silicone mold is removed from the casting box after the silicone has hardened and cured.
Step 4: Mixing the Polyurethane Resin
There are various types of polyurethane (PU) resins to choose from, and they have different material and structural properties depending on the type of part to be manufactured. The polyurethane resin used in vacuum cast is usually heated to 40ºC before mixing.
The two-component casting resin and any preferred pigment are mixed in precise volumes and poured into the container for the machine. The mold is then returned to its position while the sprue is fixed to the mixing and pouring container.
Typically, during the automatic pouring process, the vacuum cast resin and pigment are continuously mixed and degassed in a vacuum for about 50 to 60 seconds. The liquid material is then poured into the mold under a vacuum bag to prevent air pockets. The vacuum technology ensures that the mold is bubble-free and eliminates the flow resistance that bubbles inside the mold can cause, and gravity ensures that the mold is properly filled.
Step 5: Curing and demoulding the cast object
After the resin is poured into the vacuum chamber, it is heated in the curing chamber until it cures. But the casting can be removed from the mold as soon as it hardens. Therefore, you can remove the sprue and riser and carry out finishing after the casting is completed.
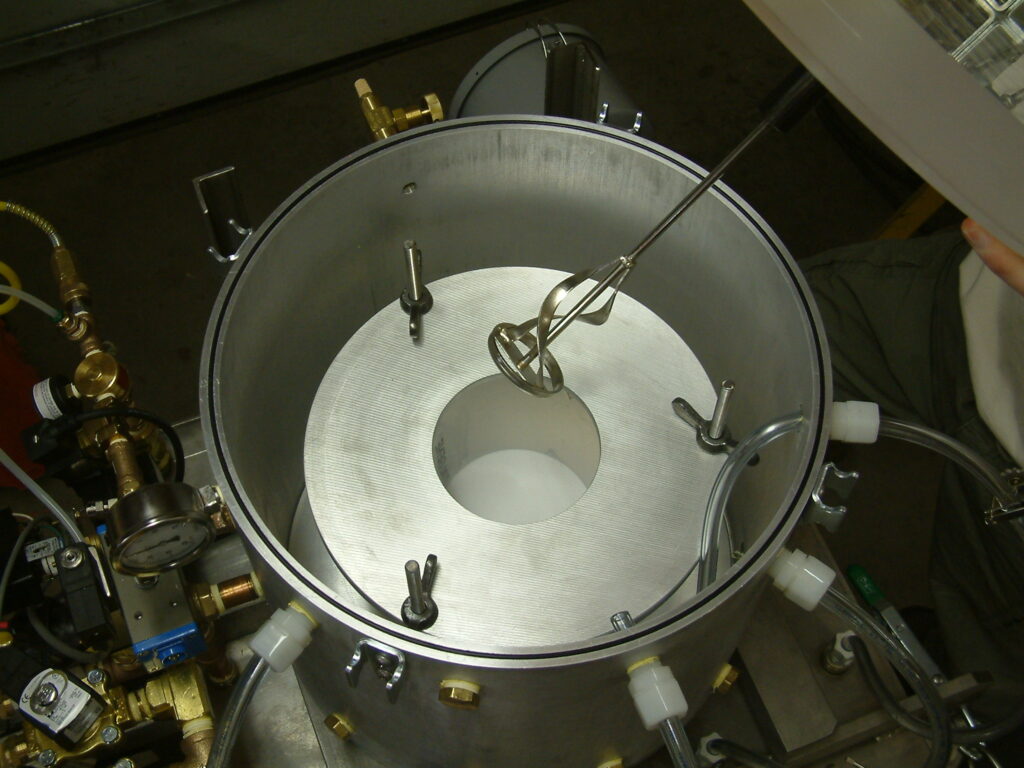
3. Advantages and Disadvantages of Vacuum Casting
Vacuum casting is a versatile production process that is ideal for small batch production prototypes and production runs.
The following are the significant advantages of vacuum casting:
1. Polyurethane casting helps achieve parts with complex shapes and features that are almost impossible to achieve with other materials.
2. There are many resins that are compatible with vacuum casting.
3. Vacuum casting is ideal for producing high-quality castings in small batches.
4. The cost of the vacuum casting process is relatively low because its molds are reusable.
5. Components made using the vacuum cast process usually fit perfectly without the need for post-processing operations such as drilling or grinding.
Although vacuum cast has many advantages, its common disadvantages include:
1. The vacuum casting process is only compatible with specific materials such as thermoplastics and rubbers.
2. It is not suitable for high-temperature applications.
3. Vacuum cast is a slow process and may not be suitable for large-scale production.
4. The type of mold used in vacuum casting may affect the quality of the prototype.
5. Shrinkage may occur, resulting in too thick or too thin castings.
4. Industrial Applications of Vacuum Casting
Vacuum casting has a variety of applications because it is a cost-effective and reliable alternative to traditional processes such as injection molding. The following are typical applications of vacuum casting in different industries:
1) Aerospace Components
Vacuum casting is a process used by engineers to create precision aerospace components. It is suitable for manufacturing aircraft parts such as fuel systems, air ducts, and exterior parts due to its repeatability, excellent precision, and ability to produce intricate details.
2) Automotive Industry
Automakers rely on silicone vacuum casting because of its ability to create highly detailed parts. It has the excellent precision and repeatability required to develop automotive parts, including exhaust systems, instrument panels, lighting lenses, intake manifolds, and body panels.
3) Medical Industry
Manufacturers in the medical industry rely on the high precision of vacuum casting to create complex parts and components such as implants and prostheses.
4) Food and Beverage Industry
Vacuum casting methods are suitable for manufacturing complex packaging components and other complex-shaped items such as bottles, cans, cups, and food containers.
5) Consumer Products
Vacuum casting is suitable for manufacturing complex consumer products such as sports equipment, mobile phone cases, sunglasses, pens, and toys. It produces high-precision products suitable for consumer use.
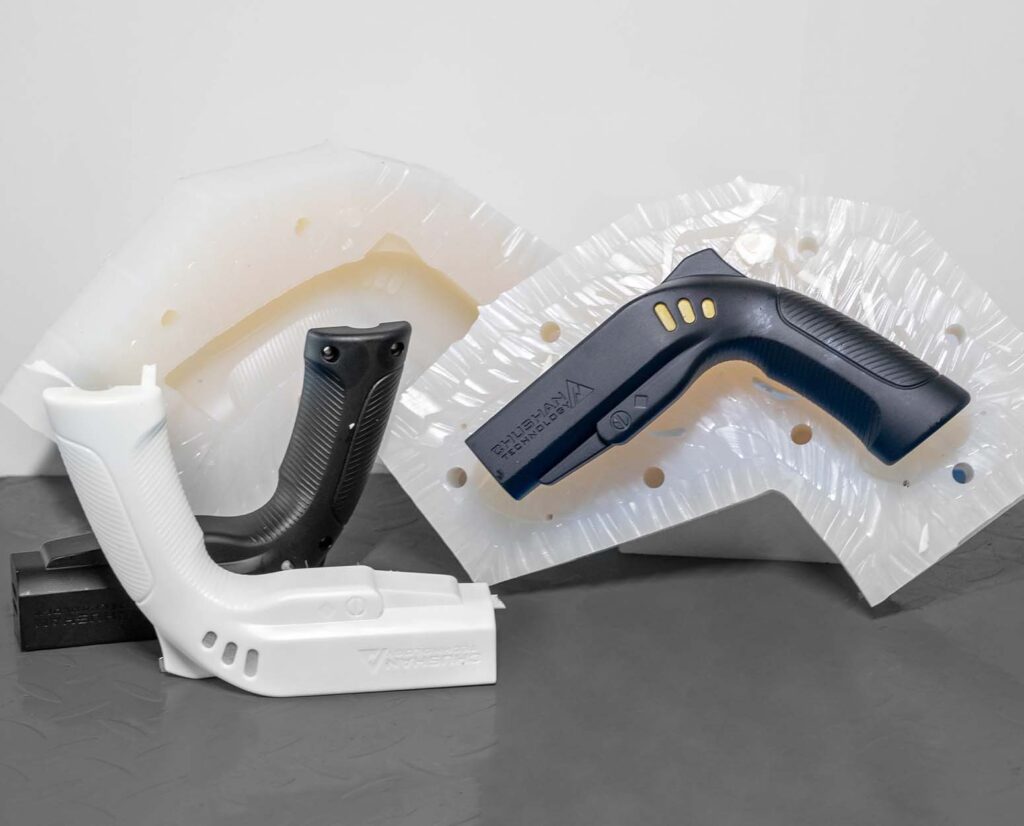
5. Vacuum Casting, Injection Molding, and 3D Printing: Comparison
Vacuum casting is a cost-effective production method that can produce fine, high-quality plastic parts with excellent surface finish.
Injection molding, on the other hand, is another common plastic part manufacturing technology that creates plastic parts by injecting molten material into a mold cavity. Injection molds are made of metals such as steel or aluminum, while vacuum casting tools are made of silicone.
Vacuum casting is more time-saving than injection molding because it does not require DFM processes. However, silicone vacuum casting is time-consuming compared to 3D printing, especially when multiple copies of the intended part are required. 3D printing is a popular additive manufacturing method that uses powder or liquid powder to create parts layer by layer.
In addition, it is helpful to consider factors such as required quantity, delivery time, tolerance requirements, and surface finish. Here are some aspects to consider when choosing between these manufacturing processes.
1. Vacuum casting is perfect for small-scale production with its tight tolerances and excellent surface finish.
2. Injection molding is ideal for large-scale production because tight tolerances are not a major requirement.
3.3D printing process is much faster than vacuum casting technology.
However, if your project focuses on speed and cost, then 3D printing will be better. At the same time, if you prioritize high precision and details, then vacuum casting is the best choice.
6. Conclusion
Vacuum casting is a cost-effective method for manufacturing fine plastic and rubber parts in small batches. Product teams often use vacuum cast parts for functional testing during the product development stage. Because silicone vacuum casting is a lower-cost and highly effective manufacturing solution, its application range is very wide.
If you are looking for an experienced casting manufacturer , Xavier is undoubtedly your best choice. The Xavier team has sophisticated equipment and can provide you with high-quality casting solutions to fully meet your personalized processing needs. If you need more information or want to discuss your needs with us, please feel free to contact us.