Advantages and application scenarios of titanium in the aerospace industry
In the field of aerospace, every breakthrough in material performance drives industry change. The application of titanium in aerospace industry has become a “key metal” supporting the development of modern aerospace technology because of its unique advantages of light weight, high strength, corrosion resistance and high temperature resistance.
From titanium alloy wings to titanium alloy engines, the application of titanium in aerospace industry has long surpassed the scope of a single material and has become a core technical path to improve aircraft performance and achieve weight reduction and efficiency. This article will deeply analyze the application logic and technological breakthroughs of titanium in aerospace industry from the dimensions of material properties, alloy classification, application scenarios and processing technology.
1.Why is titanium widely used in the aerospace industry?
The application of titanium in aerospace industry is essentially a perfect match between material properties and industry needs. Titanium and titanium alloys, with their irreplaceable comprehensive advantages, perfectly meet the stringent requirements of aerospace materials:
(1) Excellent specific strength (strength/density ratio)
The density of titanium is only 4.51 g/cm³, which is about 57% of steel and 1.6 times of aluminum, but its tensile strength can reach 500-1200 MPa, even exceeding many high-strength steels. This “lightweight and high-strength” characteristic makes the application of titanium in aerospace industry the key to reducing the weight of aviation structures.
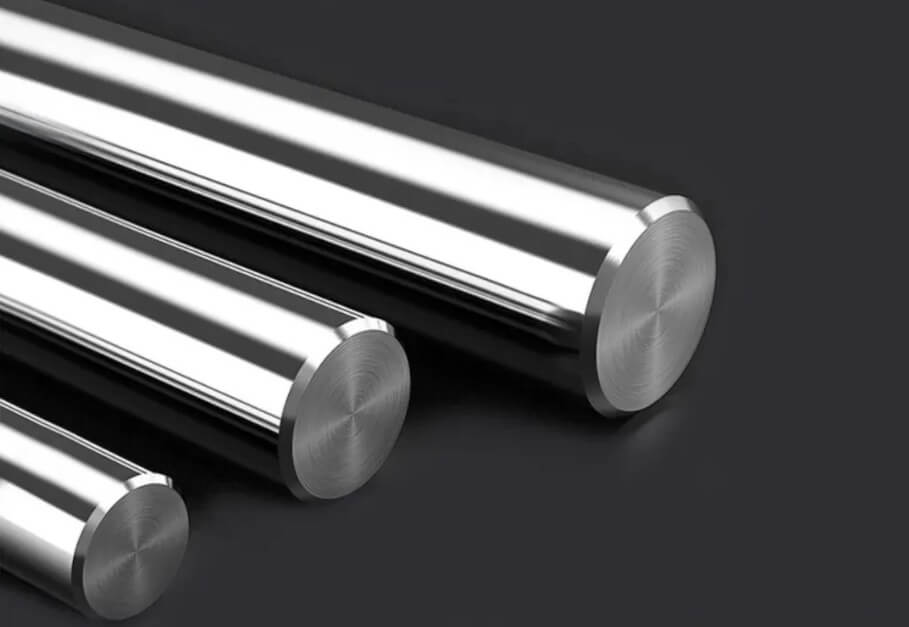
(2) Excellent corrosion resistance
A dense TiO₂ oxide film is easily formed on the surface of titanium, which shows extremely strong corrosion resistance in humid atmosphere, seawater, and acid/alkali environments. This feature makes it irreplaceable in the hot and humid environment of aircraft engines (such as the compressor section), the external skin of the fuselage (anti-salt spray corrosion) and ship aviation equipment.
(3) Good high temperature performance
Titanium alloys can work for a long time at 400-600℃ (some α-type alloys such as Ti-6Al-4V can be stable up to 500℃), far exceeding aluminum alloys (upper limit is about 200℃) and close to the level of low alloy steel. This makes it an ideal material for high temperature parts such as compressor blades and casings of aircraft engines.
(4) Fatigue resistance and fracture toughness
The fatigue strength of titanium alloys can reach 50%-60% of the tensile strength, and the fracture toughness is high, which is suitable for structural parts that bear alternating loads (such as aircraft wing beams and landing gear), reducing the risk of fatigue fracture.
(5) Biocompatibility and weldability
The biocompatibility of pure titanium makes it suitable for medical equipment inside the cabin; at the same time, titanium alloys can achieve high-quality connections through processes such as argon arc welding and electron beam welding to meet the needs of complex structure manufacturing.
2.Commonly used titanium and titanium alloy grades and characteristics in the aerospace field
Titanium alloys can be divided into three categories according to their microstructure: α type, α+β type, and β type. The application of titanium in aerospace industry shows obvious “grade customization” characteristics, and different alloys optimize performance for specific working conditions:
Alloy Type | Typical Grade | Main Alloying Elements | Key Properties | Aerospace Applications |
α Type | Ti-5Al-2.5Sn | Al, Sn | Good high-temperature stability (service temperature up to 500°C), excellent weldability | Compressor stator blades in engines, fuselage frames |
α+β Type | Ti-6Al-4V (TC4) | Al, V | Balanced comprehensive properties, high strength (σb≈900 MPa), easy to machine | Fuselage skin, wing ribs, compressor rotor blades in engines |
α+β Type | Ti-6242 (Ti-6Al-2Sn-4Zr-2Mo) | Al, Sn, Zr, Mo | Outstanding high-temperature strength (service temperature up to 550°C), strong creep resistance | High-temperature components in aircraft engines (e.g., rear-stage compressor blades) |
β Type | Ti-1023 (Ti-10V-2Fe-3Al) | V, Fe, Al | Ultra-high strength (σb≈1100 MPa), heat-treatable for enhanced properties | High-load structural components (e.g., fighter jet landing gears, wing pivots) |
Near-β Type | Ti-5553 (Ti-5Al-5V-5Mo-3Cr) | Al, V, Mo, Cr | High strength, high fracture toughness, excellent resistance to crack propagation | Military aircraft structural components, rocket engine casings |
Fire-Resistant Type | Ti-1720 (Ti-17%Nb-20%Ta) | Nb, Ta | Excellent combustion resistance, suitable for extreme environments | Rocket engine combustion chambers, thermal protection components for hypersonic vehicles |
These alloys achieve a balance between strength, toughness, and high temperature resistance by adjusting the ratio of elements such as Al, V, and Mo, ensuring that the application of titanium in aerospace industry covers the full spectrum of needs from conventional passenger aircraft to cutting-edge spacecraft.
3.Application scenarios of titanium in aerospace industry
The application of titanium in aerospace industry runs through the entire industrial chain, from the main structure of the aircraft to the core power system, covering multiple key parts:
(1) Aircraft engines (accounting for about 50% of titanium use)
Compressor parts: blades (Ti-6Al-4V), casings (Ti-6242), using their high temperature strength and corrosion resistance to replace stainless steel and reduce weight by more than 30%.
Combustion chamber and tail nozzle: Flame-retardant titanium alloys (such as Ti-1720) are used to suppress the risk of combustion at high temperatures and are suitable for supersonic aircraft.
Fasteners and shaft parts: β-type titanium alloys (such as Ti-1023) are used to make high-strength bolts and turbine shafts, which can withstand high loads and alternating stresses.
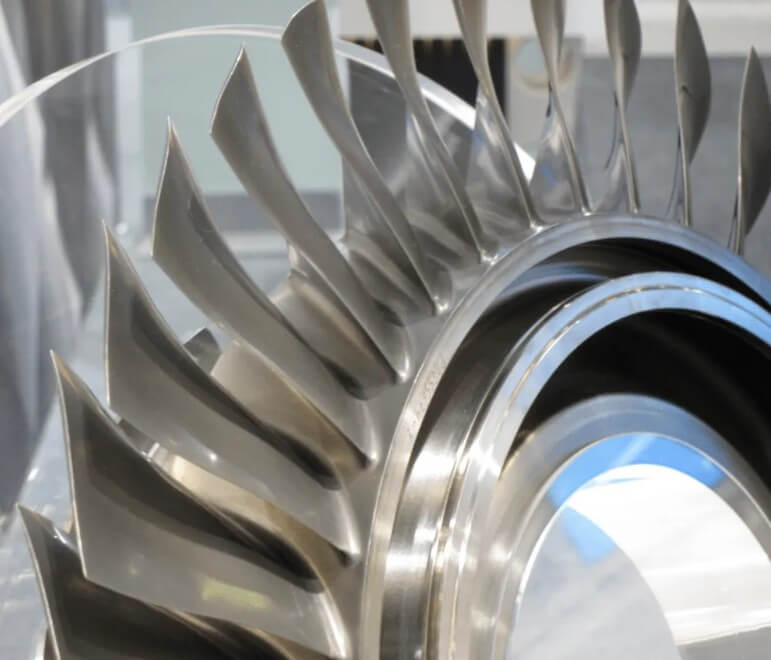
(2) Fuselage structure (accounting for about 35% of titanium usage)
Skin and bulkhead: Ti-6Al-4V is used for passenger aircraft fuselages, reducing weight while improving fatigue life; military aircraft titanium alloys account for 41%, mainly used for wing and fuselage fusion structures.
Landing gear system: Ti-1023 and other β alloys are used to manufacture landing gear through isothermal forging processes. The strength is comparable to that of ultra-high-strength steel, but the weight is reduced by 20%-30%.
Doors and window frames: Pure titanium (TA1/TA2) or low-alloy titanium (Ti-3Al-2.5V) is used to manufacture sealing structures due to its good plasticity and weldability.
(3) Spacecraft (rocket, missile, spacecraft)
Rocket engine: Titanium alloy is used for liquid hydrogen/liquid oxygen fuel tank (low temperature resistant) and thrust chamber nozzle (Ti-6Al-4V).
Missile structure: Near-β titanium alloy (such as Ti-5553) is used to make missile body to cope with aerodynamic heating and impact loads during high-speed flight.
Satellite components: Titanium alloy frames and brackets (such as Ti-6Al-4V) provide high rigidity support while reducing launch weight.
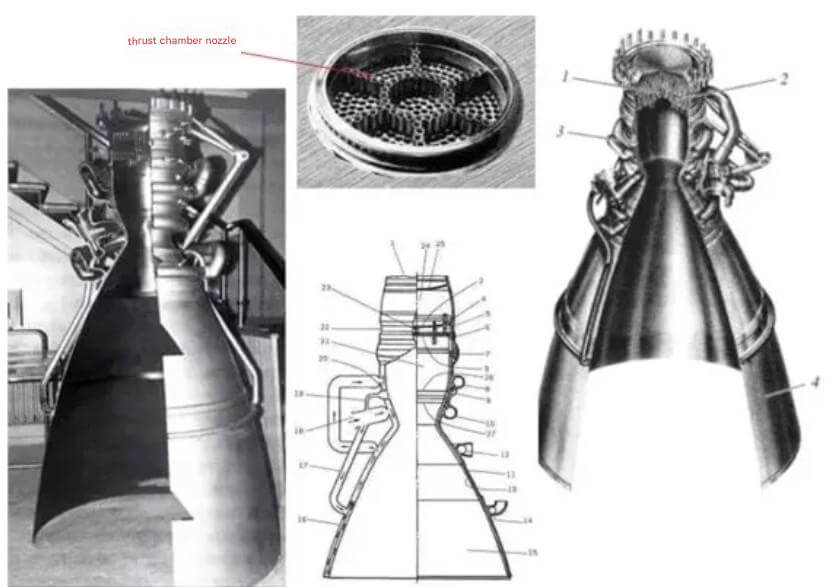
(4) Special functional components
Thermal protection system: Titanium alloy honeycomb structure or composite plate is used for the thermal protection layer of hypersonic aircraft, taking into account both thermal insulation and structural strength.
Avionics equipment: Titanium alloy shielding covers use its electromagnetic compatibility to protect precision electronic components from interference.
4.Common processing technologies and technical challenges for aviation titanium parts
The high hardness, low thermal conductivity (thermal conductivity is only 1/4 of steel and 1/15 of aluminum) and high chemical activity (easy to bond with tool materials at high temperatures) of titanium alloys make their processing difficulty significantly higher than that of steel and aluminum alloys.
The application of titanium in aerospace industry is inseparable from the support of advanced processing technology. In view of the “difficult processing” of titanium alloys, the industry has developed exclusive technical solutions:
(1) Casting process
Application scenario: Near-net forming of complex structural parts (such as engine casings and blades).
Process type:
Investment casting (lost wax method): high precision (tolerance ±0.1mm), suitable for titanium alloy turbine blades, and the problem of corrosion of the mold shell by the high melting point of titanium liquid (1668℃) needs to be solved.
Vacuum consumable arc melting (VAR): used to prepare high-purity titanium alloy ingots, reduce the content of gas impurities (such as N, H, O), and improve fatigue performance.
(2) Plastic processing (forging/rolling)
Application scenarios: Optimization of microstructure and performance of high-strength structural parts (such as landing gear and wing beams).
Process type:
Isothermal forging: Forming at a constant temperature in the β phase region or α+β phase region (such as Ti-6Al-4V at 920-950℃), avoiding work hardening caused by cold deformation and obtaining uniform fine-grained microstructure.
Hot die forging: The mold is preheated to 300-500℃ to reduce deformation resistance, which is suitable for large titanium alloy structural parts.
(3) CNC machining (turning/milling/drilling)
Application scenarios: Final forming of precision parts (such as engine blade tenons and bolt holes).
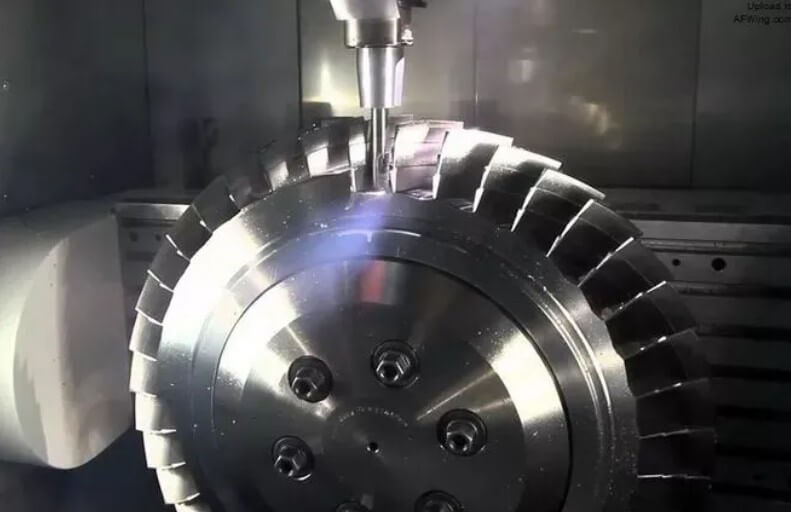
Key technologies:
Tool material: PCBN (cubic boron nitride) or coated carbide (such as TiAlN coating) is preferred, and high-speed steel (prone to adhesion and wear) should be avoided.
Cutting parameters:
Low speed and high feed: cutting speed v=30-80 m/min (only 1/3 of steel), feed rate f=0.1-0.3 mm/r, reduce the contact time between the tool and the workpiece, and reduce cutting heat.
Large cutting depth: Rough machining cutting depth ap=2-5 mm, avoid cutting in the hardened layer (the depth of the hardened layer on the surface of titanium alloy is about 0.2 mm).
Cooling and lubrication: Use high-pressure internal cooling cutting (pressure 10-20 MPa), mainly aviation kerosene or semi-synthetic cutting fluid, to inhibit the chemical reaction between titanium alloy and the tool.
(4) Powder Metallurgy (PM)
Application scenarios: complex porous structural parts (such as lightweight engine brackets), near-net-shape parts.
Process type:
Metal injection molding (MIM): titanium powder and binder mixed injection molding, suitable for small precision parts (such as avionics component housings), dimensional accuracy can reach ±0.05mm.
Selective Laser Melting (SLM): 3D printing technology uses laser to melt titanium alloy powder layer by layer to directly manufacture topologically optimized structures (such as hollow blades). This technology promotes the application of titanium in the aerospace industry to move towards “lightweight and integration”.
5.Summary
The application of titanium in aerospace industry has always evolved with technological breakthroughs. This “space metal” continues to break the “weight-strength-environment” contradiction in aircraft design with its unique performance code, and has become the core material that supports the aerospace industry to continuously surpass its limits.
With the emergence of new alloys and processing technologies, the application of titanium in aerospace industry will surely open up a broader imagination space in the fields of hypersonic flight and deep space exploration.