The Advantages of Precision CNC Components
Precision CNC components have revolutionized the manufacturing industry by offering numerous advantages over traditional machining methods. One of the key benefits of using precision CNC components is the increased efficiency and productivity they bring to the production process.
Faster and more precise
Unlike manual machining, which relies on a human operator to control cutting tools, CNC machine tools are controlled by computer programs. Automation while also enabling uninterrupted continuous operation not only eliminates the possibility of human error but also ensures that each component is machined to the precise specifications required. As a result, manufacturers can produce high-quality parts and improve product efficiency faster and without interruption.
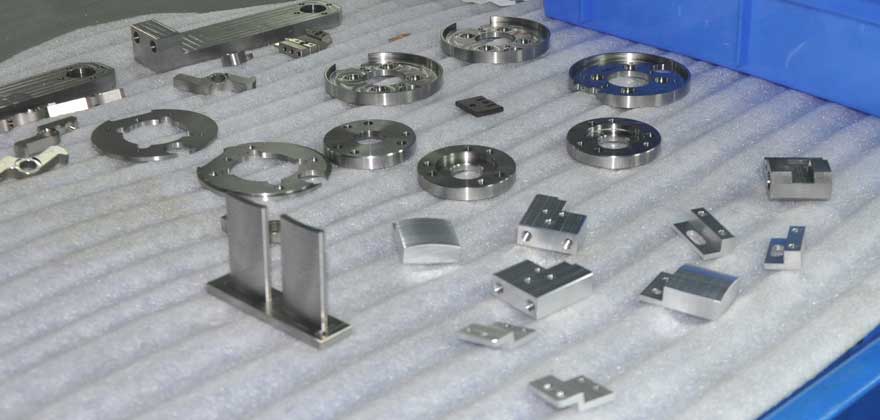
Repeatability and consistency
Once a CNC program is created for a specific component, it can be used repeatedly to produce identical parts. This eliminates the need for manual adjustments and reduces the risk of variations in the final product. Manufacturers can rely on CNC machines to consistently produce parts that meet the required specifications, resulting in a more streamlined production process and higher overall productivity.
Complex and detailed design
CNC machines are capable of performing multiple operations simultaneously, such as milling, drilling, and turning, with high precision and accuracy. This opens up a world of possibilities for manufacturers, enabling them to create intricate parts with tight tolerances and complex geometries. The ability to produce such complex designs not only enhances the aesthetic appeal of the final product but also improves its functionality, leading to increased customer satisfaction and market competitiveness.
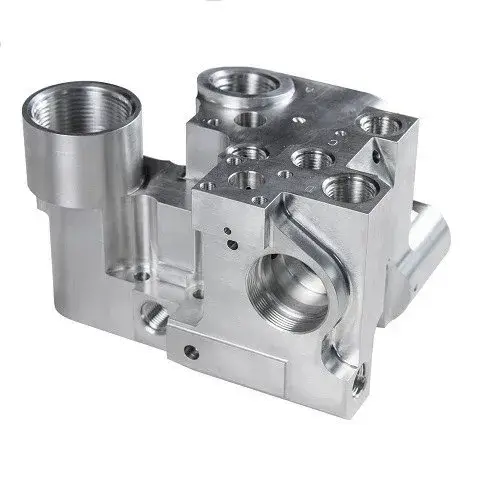
Reduced need for manual labor
CNC machines are highly automated and require minimal human intervention. Once the program is set up and the machine is running, operators can focus on other tasks, such as quality control or machine maintenance. This not only frees up valuable human resources but also reduces the risk of human error, further enhancing efficiency and productivity.
Improve material utilization
CNC machines are programmed to optimize the cutting path and minimize waste. This means that manufacturers can maximize the use of raw materials, reducing costs and minimizing environmental impact. By reducing material waste, precision CNC components contribute to a more sustainable manufacturing process, aligning with the growing demand for environmentally friendly practices.
Adapting to market changes
With traditional machining methods, retooling and reprogramming can be time-consuming and costly. However, CNC machines can be easily reprogrammed to produce different components, allowing manufacturers to adapt to new product requirements or customer preferences with minimal downtime. This flexibility and agility in production contribute to increased efficiency and productivity, giving manufacturers a competitive edge in the market.
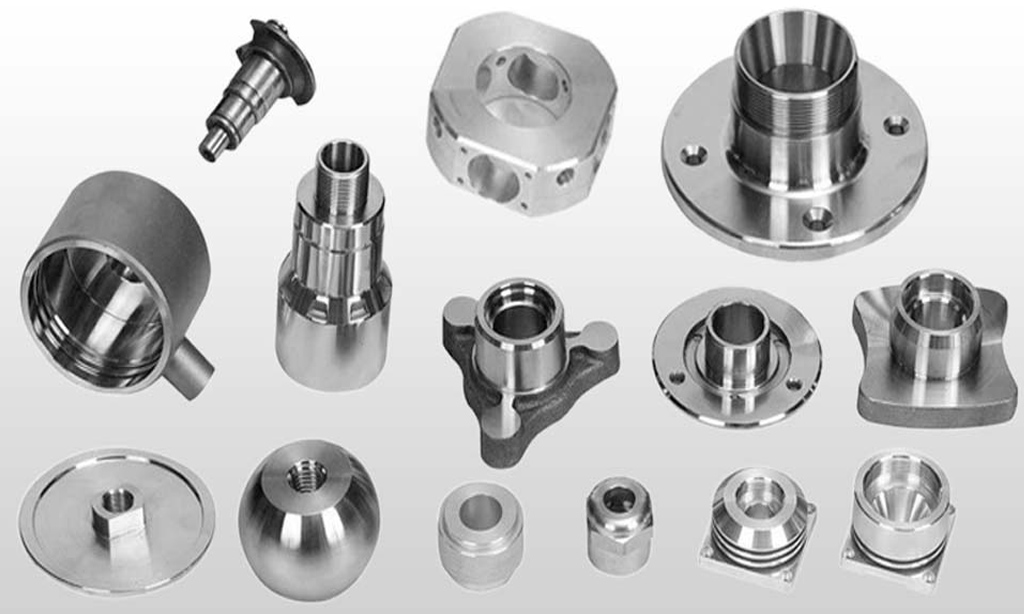
In conclusion
precision CNC components offer numerous advantages, particularly in terms of increased efficiency and productivity. From faster and more accurate machining to greater repeatability and consistency, CNC machines revolutionize the manufacturing process. The ability to produce complex designs, reduced need for manual labor, improved material utilization, and quick response to market demands further enhance the benefits of precision CNC components. As the manufacturing industry continues to evolve, precision CNC components will undoubtedly play a crucial role in driving efficiency and productivity to new heights.