Stainless Steel: A Guide to Processing
Stainless steel is a versatile and durable material used in a variety of industries, including construction, automotive, and manufacturing. Its unique properties make it an excellent choice for applications that require strength, corrosion resistance, and aesthetics. However, machining stainless steel requires careful consideration and following specific techniques to ensure the best results.
In this article, we will explore the basics of stainless steel machining and provide valuable insights for those who want to work with this extraordinary material.
Stainless Steel Processing Process
The first step in stainless steel machining is to choose the right grade. The metal is available in a variety of grades, each with its own unique properties and characteristics. The most common grades include 304, 316, and 430, which vary in composition and performance. It is essential to select the correct grade based on the specific requirements of the application to ensure the desired results.
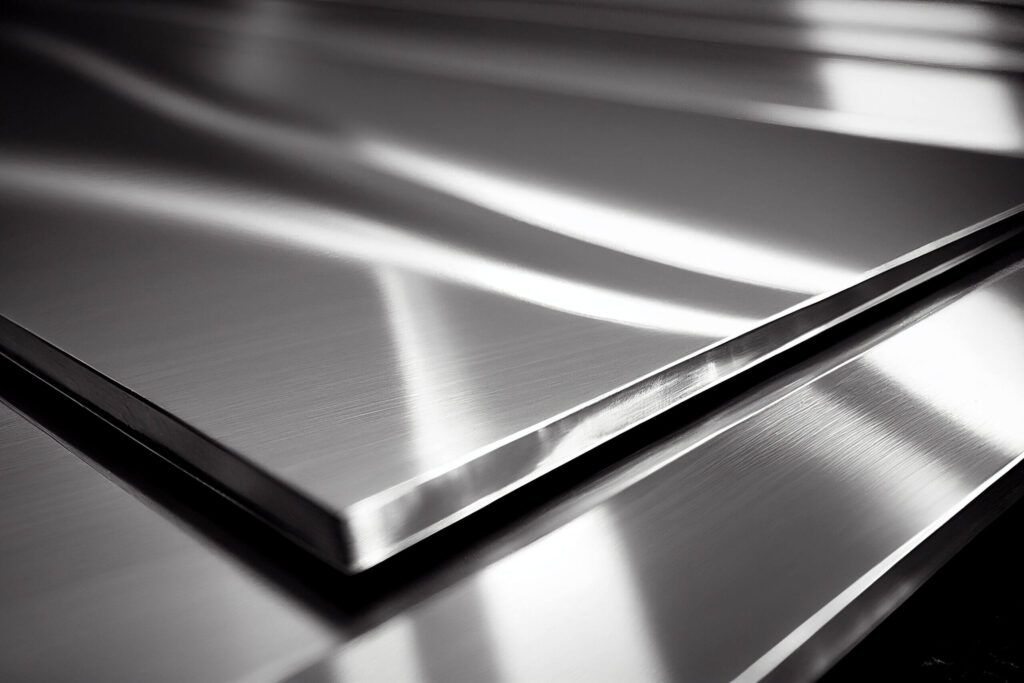
Once the grade has been determined, the next step is to consider the various machining techniques available. Stainless steel can be machined using a variety of methods, including cutting, forming, welding, and finishing. Each technique requires specific tools and expertise to achieve the desired results. For example, cutting the metal can use a variety of methods such as shearing, sawing, or laser cutting, depending on the thickness and complexity of the material.
Stainless steel forming involves shaping the material into the desired shape. This can be achieved through processes such as bending, rolling, or stamping. It is also worth noting that the metal has a higher work hardening rate than other metals, which means that it becomes harder and more difficult to form when it is machined. Therefore, proper techniques and equipment must be used during machining to avoid cracking or damage to the material during the forming process, resulting in machining failure.
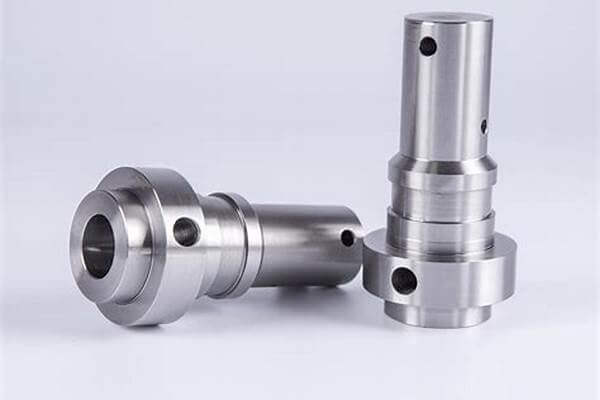
Due to the unique properties of this metal, welding stainless steel requires expertise and skills. The metal has low thermal conductivity and high thermal expansion, making it prone to deformation and bending during the welding process. To overcome these challenges, techniques such as TIG (Tungsten Inert Gas) welding or MIG (Metal Inert Gas) welding are often used. These methods allow for precise control of heat input and minimize the risk of deformation.
Finishing is the final step in the processing of this metal, and it plays a vital role in enhancing the material’s appearance and corrosion resistance. Common finishing techniques include polishing, grinding, and passivation. Polishing stainless steel produces a smooth and reflective surface, while grinding removes any blemishes or burrs. Passivation, on the other hand, involves treating the surface with a chemical solution to remove contaminants and promote the formation of a protective oxide layer.
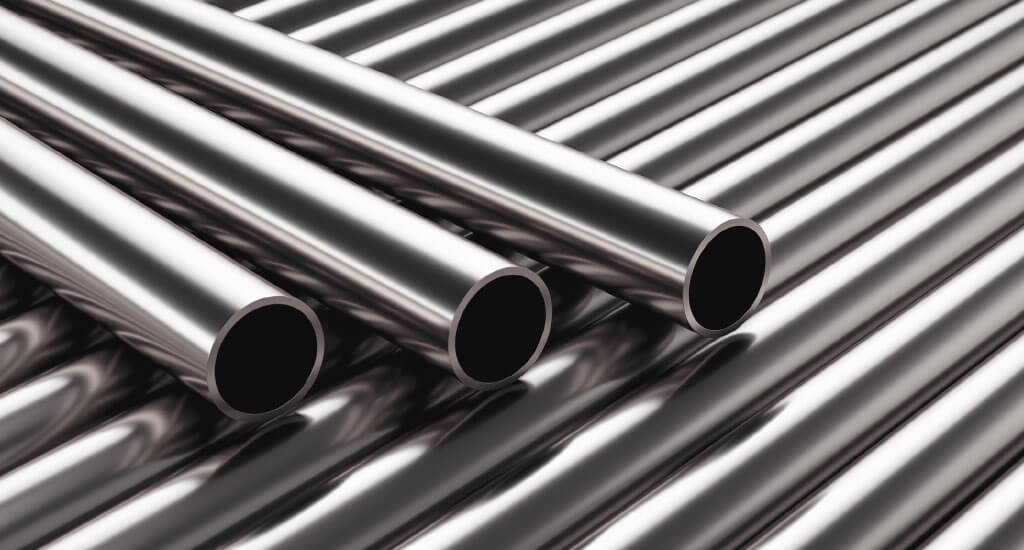
In summary, stainless steel machining requires careful consideration and adherence to specific techniques to achieve the best results. Selecting the right grade, understanding the various processing methods, and using the correct tools and expertise are essential to successfully processing stainless steel. By following these guidelines, individuals and industries can fully realize the potential of stainless steel and enjoy its many benefits, including strength, corrosion resistance, and aesthetics.