Metal Die Castings: Effective Ways to Reduce Shrinkage
Metal die castings are widely used across industries due to their high strength, durability, and cost-effectiveness. However, a common problem faced by manufacturers is shrinkage. Shrinkage occurs when metal solidifies and shrinks, resulting in defects and dimensional inaccuracies in the final product. To ensure high quality of castings, it is crucial to implement effective techniques to reduce shrinkage.
In this article, we will explore some proven methods to help minimize shrinkage in metal die castings.
1.Gating and Riser Systems
One of the most effective techniques to reduce shrinkage is to use a proper gating and riser system. Gating refers to the process of controlling the flow of molten metal into the die cavity, while risers involve the use of additional channels to feed molten metal into the casting.
By designing an optimized gating and riser system, manufacturers can ensure a smooth and controlled flow of metal, thereby minimizing the potential for shrinkage. The technique requires careful analysis of the casting geometry, material properties, and process parameters to determine the ideal location and size of the gates and risers.
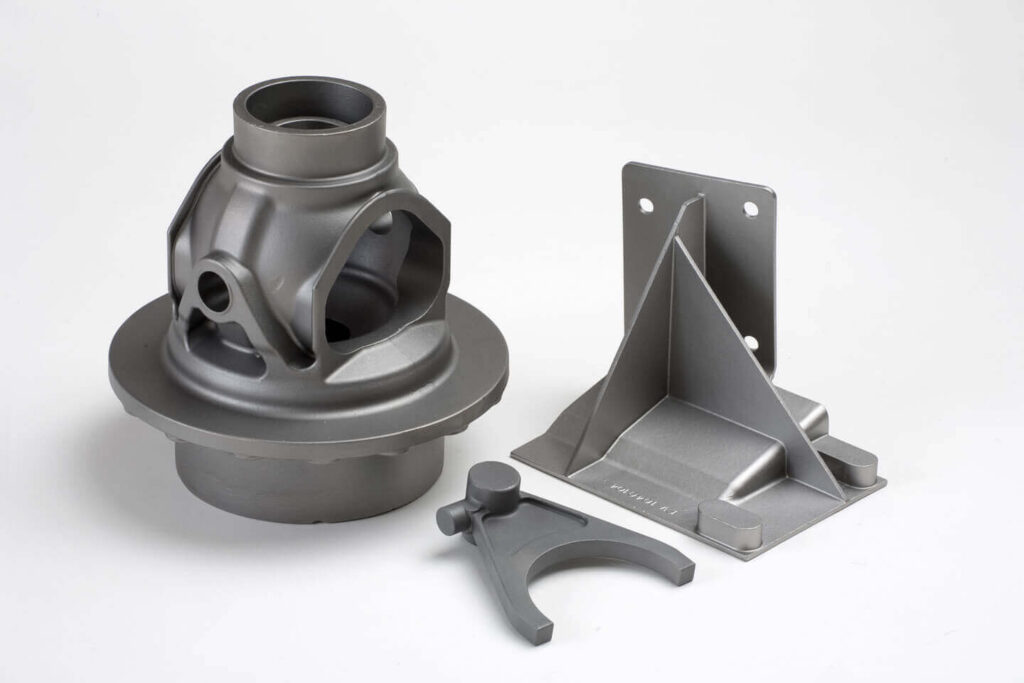
2.Using Alloy Modifications
Another way to reduce shrinkage is to use alloy modifications. Different alloys have different solidification characteristics, and some are more susceptible to shrinkage than others. By selecting alloys with a lower tendency to shrink, manufacturers can significantly reduce the occurrence of shrinkage defects.
Also, alloy modification may involve adding certain elements or adjusting the composition to improve the metal’s fluidity and solidification behavior. This approach requires a thorough understanding of the alloy’s characteristics and the specific requirements of the casting.
3.Controlling the cooling rate during solidification
Because rapid cooling can lead to excessive shrinkage, while slow cooling can lead to the formation of large grains and pores. By implementing appropriate cooling techniques, such as cooling channels or controlled cooling media, manufacturers can achieve a balanced cooling rate that minimizes shrinkage.
And when determining the cooling strategy, the geometry and thickness of the casting must be considered to ensure uniform solidification and minimize shrinkage defects.
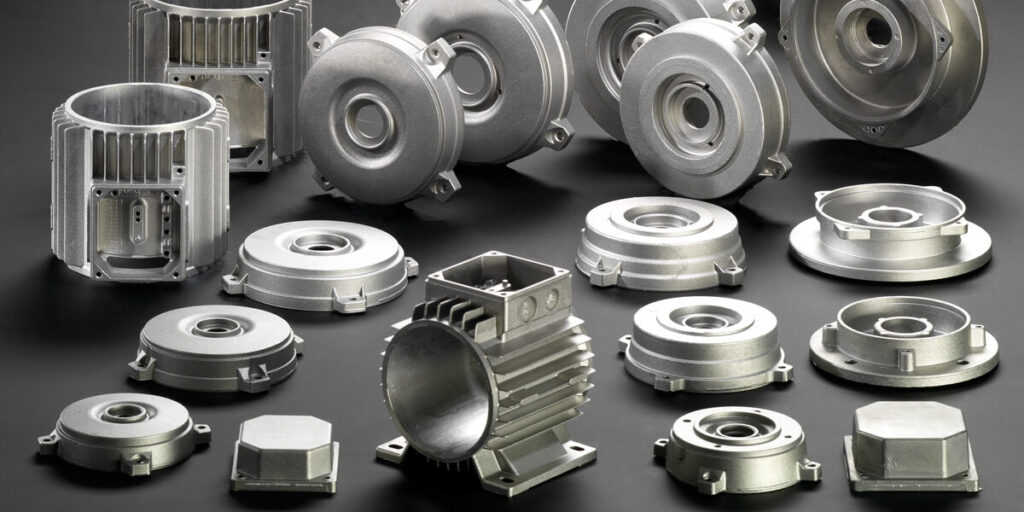
4.Mold coatings
In addition to these techniques, the use of mold coatings can also help reduce the shrinkage of metal die castings. Mold coatings act as a barrier between the molten metal and the mold surface, preventing excessive heat transfer and promoting controlled solidification. These coatings can be made of a variety of materials, such as ceramic or graphite, and are applied to the mold cavity before casting.
By selecting the right mold coating and applying it correctly, manufacturers can improve the surface finish and reduce shrinkage defects in the final product.
5.Process Optimization
Process optimization plays a vital role in reducing shrinkage in metal die castings. By carefully analyzing and adjusting process parameters, such as pouring temperature, mold preheating, and cycle time, manufacturers can achieve optimal solidification conditions and minimize shrinkage.
Process optimization requires continuous monitoring and analysis of casting defects to identify areas for improvement and implement corrective actions.
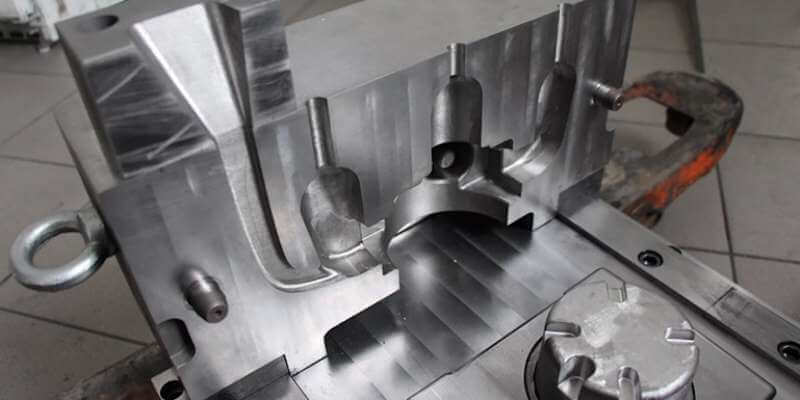
In summary, reducing shrinkage in metal die castings is critical to ensuring a high-quality product. By implementing effective techniques, such as proper gating and riser systems, alloy improvements, controlled cooling, mold coatings, and process optimization, manufacturers can minimize shrinkage defects and achieve dimensional accuracy in castings. It is critical to consider the specific requirements of each casting and continuously improve the manufacturing process to achieve the best results.