1.Aluminum Machining Overview
Aluminum machining plays an important role in the modern industrial field. Aluminum has become the metal of choice for many machining scenarios due to its good machinability, and its machined parts are not only durable but also beautiful in appearance. However, aluminum machining also faces some challenges.
The machinability of aluminum is limited by certain problems, including long and sticky obstructive chips; chip entanglement; rough thread surface; over-machining appearance and straightness problems.
Fortunately for those in the machining industry, engineers and metallurgists are constantly working to find solutions to improve the machinability of aluminum and its various alloys – by improving the material itself, improving processing methods and selecting suitable alloys.
2.Metallurgy and Aluminum Machining
One way to improve Aluminum Machining performance is to optimize the metallurgical process. The current widely used direct press aluminum extrusion method, namely forward extrusion, can quickly produce large pieces of aluminum, but there are problems such as uneven force leading to inconsistent grains, which may make one end of the aluminum billet unusable.
The indirect press and reverse extrusion process can produce more consistent and higher-quality workpieces. This process uses a rod to push the container and billet, and the punch and die remain stationary, which reduces friction and reduces the possibility of cracking, but is less versatile than forward extrusion.
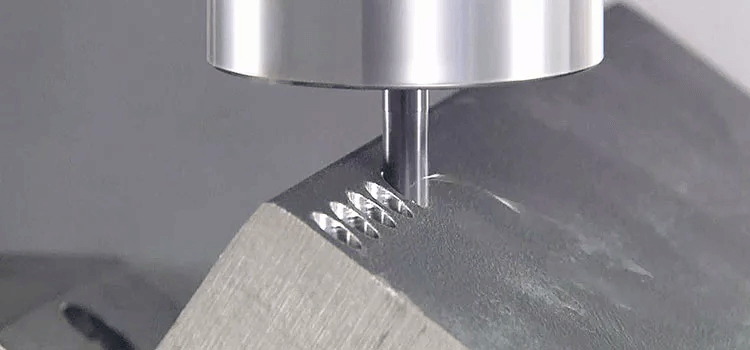
3.The Effect of Alloy Selection on Aluminum Processing
Different aluminum grades have different machinability characteristics. A6061 is a common aluminum alloy used in machining, with good mechanical properties and corrosion resistance for machining parts and consumer products, but difficult chips to break in certain tempering conditions.
Other alloys, such as A6042 and A6262, have material properties that improve aluminum machining performance. A6042 produces smaller chips than A6061, while A6262 was developed specifically for machining applications, with small, curly chips, good finishing characteristics, and heat treatability.
4.Importance of Aluminum Machining Tools
Machinability of aluminum can also be improved by selecting the right tools and machining techniques. Generally speaking, aluminum is better suited to tools made of tool steel, high-speed steel, carbide and diamond rather than ceramic or synthetic materials.
Maintaining cutting tools has a significant impact on aluminum machining performance. Keeping cutting edges sharp, finely grinding cutting edges, using proper rake angles, and coolant feed systems ensures optimal aluminum machining while extending tool life. Keep chips away from the workpiece or into a chip breaker during machining, especially when machining less machinable alloys.
5. Conclusion
Aluminum processing is essential in modern industry. Although it faces challenges, improving aluminum processing performance can start from metallurgy, alloy selection and tool maintenance. Taking these factors into consideration can help improve production efficiency and product quality.
If you need an experienced processing manufacturer, Xavier is your best choice. The Xavier team is well-equipped to provide high-quality processing solutions to meet your personalized processing needs. Please feel free to contact us.