Guide to Deburring Aluminum Parts
Deburring is a crucial step in the manufacturing process of aluminum parts. It involves removing the sharp edges, burrs, and rough spots that are left behind after the machining or cutting process. While it may seem like a minor detail, deburring plays a significant role in ensuring the quality and functionality of aluminum parts.
1.Analysis of the important reasons for deburring aluminum parts
One of the primary reasons why deburring aluminum parts is important is safety. Sharp edges and burrs can pose a risk to workers who handle these parts. If not properly deburred, these edges can cause cuts and injuries. By removing these sharp edges, deburring helps create a safer working environment.
In addition to safety, deburring also improves the overall quality of aluminum parts. Burrs and rough spots can affect the fit and function of the parts, leading to issues such as misalignment or improper assembly. Deburring ensures that the parts fit together smoothly and function as intended, enhancing the overall performance of the product.
Furthermore, deburring aluminum parts can also improve their aesthetic appeal. Burrs and rough edges can make the parts look unfinished and unprofessional. By removing these imperfections, deburring helps create a polished and visually appealing final product.
2.Methods of Deburring Aluminum
There are several methods available for deburring httaluminum parts, each with its own advantages and limitations. One common method is manual deburring, which involves using handheld tools such as files, sandpaper, or deburring knives to remove the burrs and rough spots. This method is suitable for smaller parts or areas that are difficult to access with automated equipment. However, manual deburring can be time-consuming and labor-intensive.
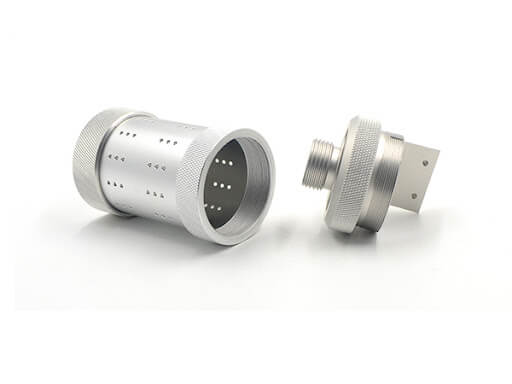
Another method is mechanical deburring, which uses machines or equipment to remove burrs and burrs. This method is more efficient and can handle larger volume parts. At the same time, mechanical deburring can also be completed through processes such as roller grinding, vibration finishing or sandblasting. These methods use abrasive media or compounds to remove burrs and smooth the surface of the part. And because mechanical deburring is faster and more consistent than manual deburring, it is the first choice for many manufacturers.
Chemical deburring is another option for deburring aluminum parts. This method involves using chemical solutions or baths to dissolve the burrs and rough spots. Chemical deburring is particularly effective for complex or intricate parts that are difficult to deburr using other methods. However, it requires careful handling of the chemicals and proper disposal to ensure environmental safety.
Regardless of the method chosen, it is essential to carefully inspect the deburred parts to ensure that all burrs and rough spots have been removed. Any remaining imperfections can compromise the quality and functionality of the parts.
3.Conclusion
In conclusion, deburring aluminum parts is a critical step in the manufacturing process. It improves safety, enhances the quality and functionality of the parts, and contributes to their aesthetic appeal. Whether through manual, mechanical, or chemical methods, deburring ensures that aluminum parts are free from sharp edges, burrs, and rough spots, resulting in a superior final product.