Analysis of the principle and applicability of chemical deburring aluminum
Have you ever encountered the following problems: The inner holes of aluminum parts cannot be cleaned of burrs? Mechanical processing is prone to surface damage? In fact, more and more engineers are beginning to use chemical deburring aluminum technology to solve this series of problems. So how does chemical deburring aluminum accurately remove burrs without damaging parts? This article will reveal the answers to you one by one.
1.What are the principles and applicable scenarios of chemical deburring?
Chemical deburring is a process of selectively dissolving metal burrs with acidic or alkaline solutions to achieve the purpose of smoothing the surface of metal parts. Its principle is based on the fact that the burr part is sharper in shape, has a larger surface area, and has weaker adhesion, so it is more easily corroded than the parent material in chemical reactions.
Chemical deburring, a surface treatment method, does not rely on mechanical contact, so it can avoid scratches or deformation of parts caused by mechanical action. It is suitable for soft metals such as aluminum, and is particularly suitable for parts with fine burrs, inner holes, cross holes or complex shapes after processing, such as aerospace parts, precision instruments, medical equipment and microelectronic components.
2.What are the common chemical formulas and usage conditions for chemical deburring of aluminum?
For aluminum, a commonly used chemical deburring formula is 84.5% phosphoric acid, 10% acetic acid, 5% nitric acid, and 0.5% copper nitrate. This solution reacts more actively at 80 to 100 degrees Celsius, and the processing time is generally controlled between 10 and 15 minutes.
Chemical deburring of aluminum usually uses a solution system based on phosphoric acid. The following table will show you the content of the four solutions of phosphoric acid, acetic acid, nitric acid, and copper nitrate, as well as their respective functions:
Component | Content (by volume) | Function |
Phosphoric Acid (H₃PO₄) | 84.5% | Main corrosive agent; uniformly dissolves burrs |
Acetic Acid (CH₃COOH) | 10% | Controls corrosion rate; improves surface finish |
Nitric Acid (HNO₃) | 5% | Activates the aluminum surface; enhances reactivity |
Copper Nitrate (Cu(NO₃)₂) | 0.5% | Promotes electron transfer; improves efficiency |
After you get the solution formula, you also need to pay special attention to the following:
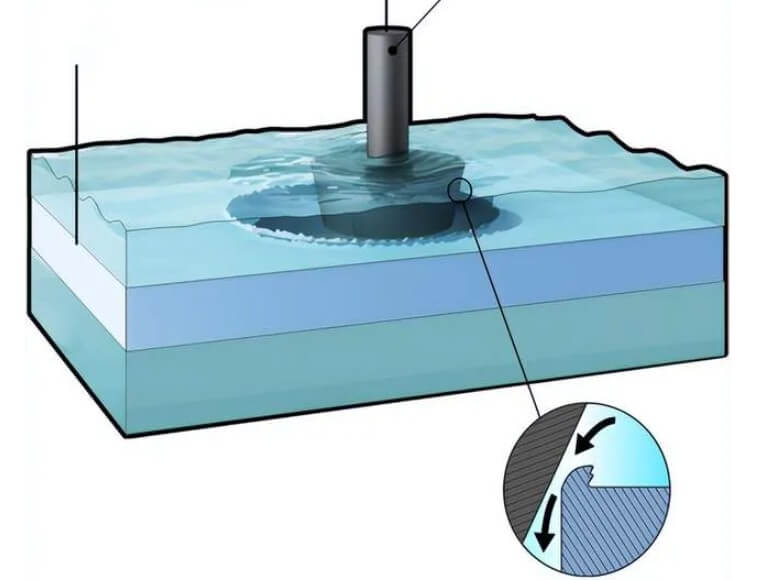
Before formal deburring, aluminum parts need to be thoroughly degreased and cleaned to ensure that there is no oil or oxide layer on the surface. After corrosion is completed, the workpiece needs to immediately neutralize the residual acid, which is usually neutralized with sodium carbonate solution, and then rinsed with pure water and dried. As for the specific formula and time, they need to be adjusted appropriately according to the workpiece structure and burr degree.
3.How is the treatment effect of chemical deburring aluminum? Will it affect the surface of aluminum parts?
The biggest advantage of chemical deburring aluminum is that it can remove tiny burrs evenly and contactlessly, especially in areas that are difficult to handle with traditional mechanical methods, such as blind holes, microchannels, cross holes, etc. Usually, burrs in the range of 5 to 50 microns can be removed after treatment, and the overall shape of the workpiece will not be affected.
Under the premise of controlling the temperature, time and solution concentration, the surface of aluminum parts will not be corroded or discolored, nor will the finish be reduced. On the contrary, in some cases, the surface roughness can be improved. However, if the reaction time is not properly controlled, slight corrosion spots or dimensional deviations may indeed occur, so it is particularly necessary to accurately control the process parameters.
At this time, it seems how important it is to choose a high-quality surface treatment provider. We at Xavier have rich experience in aluminum deburring, and we also have diversified surface treatment services. If you have part processing and processing needs, please consult our professional engineers for details.
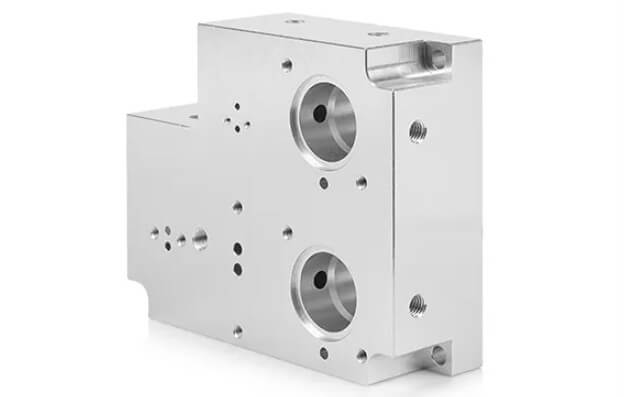
4.Are the chemicals in chemical deburring aluminum toxic? How to ensure safety and environmental protection?
Most chemical deburring solutions contain strong acids, such as phosphoric acid and nitric acid, and may also contain metal salts such as copper nitrate. These substances are corrosive, irritating and toxic to a certain extent, so you need to be extra careful when operating. You must wear acid and alkali resistant gloves, goggles, and protective clothing, and operate in a well-ventilated pickling workshop.
At the same time, the waste liquid cannot be discharged directly. It should be neutralized (such as using sodium carbonate or sodium hydroxide), heavy metal ions should be precipitated, and filtered and treated with environmental protection equipment before it can be discharged.
5.What are the advantages and limitations of chemical deburring aluminum compared with other deburring aluminum methods?
In addition to chemical deburring aluminum, common deburring aluminum methods include mechanical method, combustion deburring method and electrochemical method. The following is an introduction to the principles and applicability of these three methods:
Mechanical method (vibration, polishing, sandblasting)
Mechanical deburring is the most common method. Its principle is to use external force to apply friction, impact or cutting action to the surface of the workpiece to remove the burrs.
For example, vibration deburring is to put the parts together with abrasives and chemical additives into a vibration grinder, and remove sharp corners and burrs by relative movement; polishing is to grind the surface with a grinding wheel or abrasive paste; sandblasting is to use high-speed sand flow to impact the edge of the part to peel off the protrusion.
Mechanical deburring is suitable for large quantities of parts with relatively simple structures, but it is easy to cause deformation or scratches on the edge of the workpiece due to contact processing, and is not suitable for high-precision parts.
Combustion deburring
Combustion deburring usually refers to deburring by using instant high-temperature combustion or explosion. The principle is to place the workpiece in a closed container and pass combustible gases such as hydrogen and oxygen. After ignition, a high temperature of 2500 to 3000 degrees Celsius is generated instantly, so that the tiny burrs are quickly melted or vaporized due to their small mass and low heat capacity, while the main parts are not affected due to their large volume.
This method is highly efficient and suitable for materials such as stainless steel and cast iron, but it is not suitable for metals with low melting points and easy deformation such as aluminum. After treatment, surface oxidation, discoloration and even structural damage may occur.
Electrochemical method (such as electrolytic machining, electrochemical polishing)
Electrochemical deburring uses the principle of electrolysis, that is, the workpiece is used as the anode and the tool is used as the cathode in the electrolyte. After power is turned on, the protruding parts are removed through the anodic dissolution reaction. Its core mechanism is based on the electrolytic reaction: the current density is more concentrated at the tip of the burr, resulting in the metal being dissolved preferentially there, thereby achieving automatic flattening.
Electrochemical deburring has high precision and strong controllability, and is especially suitable for complex structures such as micropores, threads, and cross holes, and will not produce mechanical stress or thermal deformation. It is suitable for precision parts that have high requirements for form and position tolerances and cannot be contacted for processing. The disadvantage is that the equipment cost is high and the process parameter control requirements are strict.
The above four methods of deburring metal parts, chemical deburring aluminum, mechanical deburring, combustion deburring, and electrochemical deburring, have been fully introduced. The following table will compare the advantages and limitations of these four methods:
Method | Advantages | Limitations |
Chemical Method | Can handle complex shapes; No mechanical stress; High batch consistency | High requirements for equipment and operation; Need to treat waste liquid |
Mechanical Method (vibration, brushing, sandblasting) | Low cost; Suitable for rough processing of large workpieces | Not suitable for fine burrs or complex internal structures |
Thermal Method (explosion, combustion) | Fast; Suitable for certain alloy parts | Excessively high temperature may cause aluminum to deform or oxidize; Not recommended |
Electrolytic Method (electrochemical deburring) | Uniform deburring; Strong controllability | High cost; Only applicable to conductive materials |
Conclusion: Chemical method is the best choice for deburring high-precision and complex structural aluminum parts, especially for aerospace, medical equipment and other fields.
Of course, these are some post-processing methods for deburring. Perhaps you still have some doubts, isn’t it more convenient to eliminate burrs or reduce the occurrence of burrs directly during the processing? Yes, it is true, but it is a challenging task that requires strict control during the processing.
6.Are there any industry standards or relevant technical specifications for chemical deburring aluminum?
Some users may be very concerned about this issue. At present, there is no unified standard for chemical deburring aluminum at the international or national level. For example, ISO or ASTM does not clearly specify the detailed parameters of the process.
However, many high-end manufacturing companies will formulate internal control standards based on the processing requirements of their own products. For example, our Xavier has a complete process flow card, chemical liquid ratio instructions, deburring depth control standards, etc. In addition, for some customers in the aviation and medical industries, if they have requirements, we can also provide consistency reports and process stability certification.
7.Summary
Whether in terms of deburring effect, process accuracy or processing difficulty, chemical deburring has demonstrated its unique value in high-end aluminum processing. Of course, it is not omnipotent. Only by selecting it reasonably according to the product structure and quality requirements can the maximum process advantage be brought into play. If you are looking for a more efficient and stable aluminum deburring solution, chemical treatment technology is worth incorporating into your process route.
FAQs:
Does chemical deburring aluminum affect the dimensional accuracy of parts?
No. Chemical deburring mainly removes extremely small burrs and protrusions on the surface, and has little effect on the main size of the part, usually within the micron level. As long as the process parameters are properly controlled, the shape and tolerance of the part will not be damaged.
Can chemical deburring aluminum remove burrs in inner holes or blind holes?
Yes. Chemical deburring aluminum has good comprehensiveness and is particularly suitable for removing burrs in complex locations such as blind holes, inner cavities, and cross holes. This is an ideal supplement to areas that cannot be reached by mechanical deburring.
What is the optimal operating time for chemical deburring aluminum?
Depending on the actual burr thickness and formula concentration, one treatment usually takes 10-15 minutes. Some people use fluidized treatment to achieve ideal results within 10 minutes. It is recommended to test on a small sample first to determine the optimal time.
Is chemical deburring applicable to all aluminum alloys?
Not completely applicable. Although most aluminum alloys can be chemically deburred, some high-silicon or special-ratio aluminum alloys may have uneven reactions or surface discoloration problems in specific solutions. Therefore, it is recommended to conduct a small sample test to confirm the feasibility before formal processing.
How to clean the workpiece after chemical deburring?
After deburring, it must be neutralized with alkali solution first, then rinsed repeatedly with deionized water to ensure that the residual acidic substances are completely removed, and finally hot air or natural drying. Inadequate cleaning can easily cause subsequent corrosion or use risks.
Is chemically deburred aluminum more suitable for batch processing than mechanically deburred aluminum?
For complex structures or blind hole parts, chemical methods are more efficient because they can process multiple parts at the same time and do not require manual operation. However, mechanical deburring still has advantages in surface finishing and removing thick burrs, and the two can be used complementary.