What is CNC Milling? Learn About This Useful Manufacturing Method
CNC milling is a CNC process that involves using a rotating tool to remove portions of a block of material or a workpiece until the desired custom shape or feature is formed. It also allows manufacturers to precisely manufacture complex parts while meeting tight tolerances. You can also learn this through the UTI CNC Machining course.
Over the years, computer numerically controlled (CNC) milling machines have evolved to produce precision parts that meet the stringent requirements of today’s demanding industries. The applications for CNC milling machines are nearly endless and cover many industries such as aerospace, automotive, robotics, and medical.
This article will take a deep dive into the nitty-gritty of CNC milling. If you want to understand the milling process, the types of milling operations, and the benefits of the process, you’ve come to the right place.
1.Key Points about CNC Milling
- CNC milling is a complex CNC machining process that involves various components working together to create precision parts with the desired surface finish.
- The CNC controller, column and base structure, power feed mechanism, axes, and tooling are all critical to achieving the accuracy and precision of the machining operation.
- CNC machining vs. manual machining depends on the complexity of the project. Going from raw material to finished parts requires programmed cutting tools and core components.
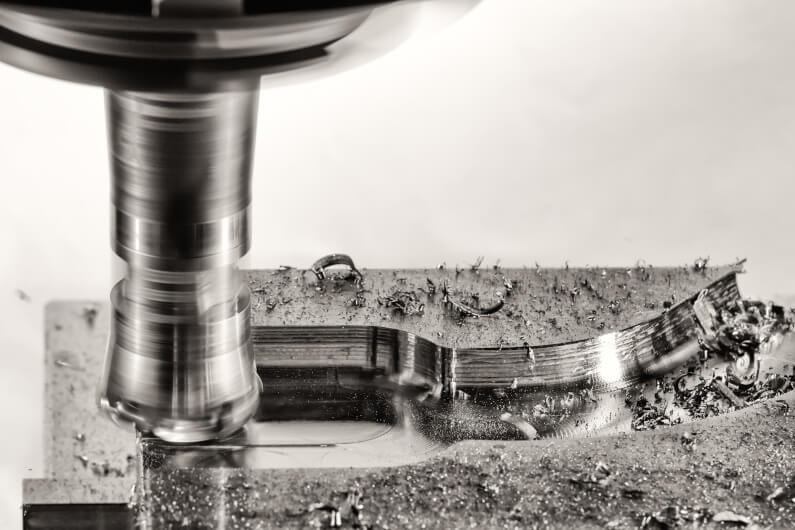
2.What is A CNC Milling Machine?
To understand what a CNC milling machine is and how it works, let’s review the basics of milling. Milling is a machining process that involves using a rotating tool to remove portions of a block of material or a workpiece until the desired custom shape or feature is made.
Traditional milling machines typically have a movable table or clamping device that holds the workpiece in place, allowing the machine operator to move the workpiece in different directions relative to the rotating tool.
Like traditional milling machines, CNC milling machines rely on a movable table and a rotating tool to remove material and make parts. But they differ in how they perform these machining operations.
CNC milling machines use computer controls to perform machining operations, while traditional milling requires manually operated rotating tools to create parts.
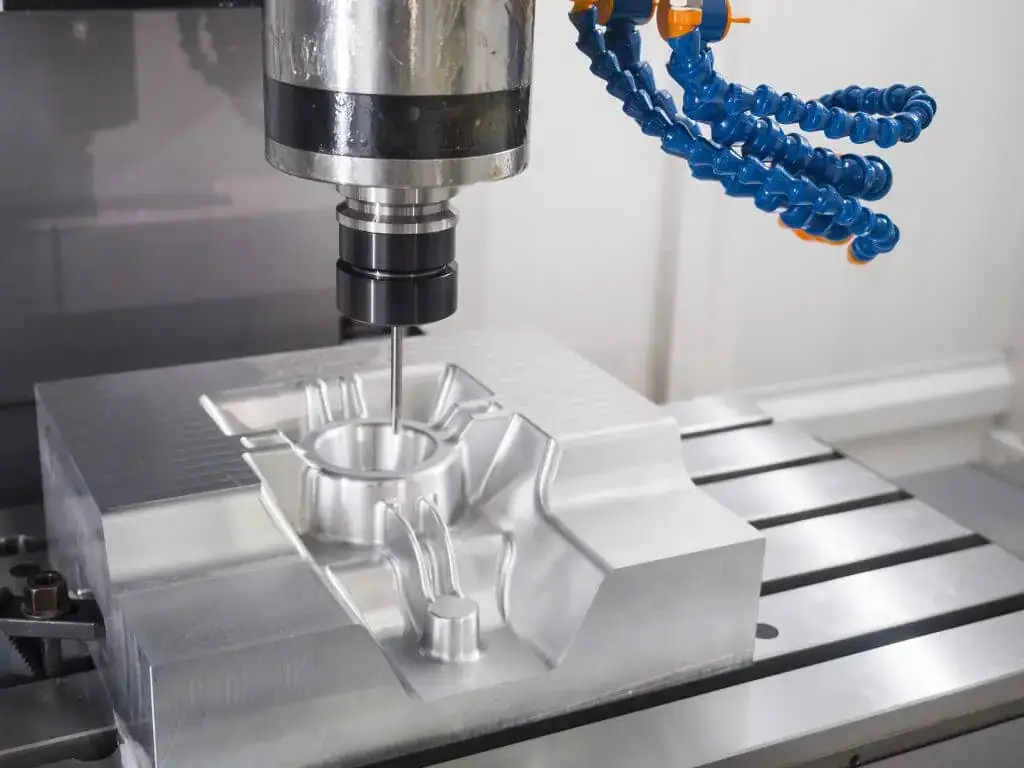
3.Explore the Core Components of a CNC Milling Machine
A CNC milling machine is an engineering marvel that combines a variety of components to transform raw materials into complex shapes and designs. The machine control unit (MCU) plays a key role in managing the movement and operation of the machine, and the core components work together to achieve efficient operation and precise CNC machine working capabilities.
CNC milling machines are composed of several major components, including:
- CNC controller
- Column and base structure
- Power supply mechanism
- Tool changer
- Worktable and T-slot
- Spindle and servo motor
- Display unit and control panel
These parts work together to ensure that the milling operation is precise and transforms raw materials into customized parts with the required surface finish.
1) The Heart of The Machine: CNC Controller
① As the brain of the machine, the CNC controller has several important functions:
- Interpret G-code instructions
- Manage the movements and operations of the factory
- Convert inputs into corresponding machine actions
- Execute commands by sending appropriate signals to stepper motors and servo motors
② The machine control unit (MCU) is a key component of CNC milling machines. It performs several important functions, including:
- Regulates the movement and operation of the milling machine according to G-code instructions
- Interprets G-code coordinates into movements performed by servo motors along the machine axes
- Controls tool changers and coolant activation
- Interprets feedback from sensors to verify the position of the tool after the move is completed
The MCU plays a vital role in ensuring accurate milling operations.
2) Pillar: Pillar and Base Structure
The pillar and base structure provide the necessary support and stability for accurate and consistent machining. These structures are usually made of materials such as epoxy granite, cast iron or aluminum, which provide the required strength and rigidity.
The design of the pillar and base structure greatly improves the accuracy of CNC milling machines, minimizing vibration and deflection during machining, thereby ensuring high-precision and accurate cutting.
In addition, the design of the pillar and base structure also affects the weight distribution of the machine, further improving its stability and accuracy.
3) Pusher: Power Feed Mechanism
The power feed mechanism ensures that the workpiece and cutting tool move accurately along the machine axis, thereby achieving precise cutting operations. The mechanism consists of the following parts:
- Knees
- Driving system
- Bed
- T-slots
All the parts work together to adjust the vertical, longitudinal and lateral feeds of the machine, including the use of vertical set screws.
While traditional CNC machine beds move along the horizontal X and Y axes, advanced 5-axis machine beds can perform rotational motion along the X and Y axes for more precise control.
This versatility enables CNC machines to handle a wide range of cutting and forming tasks, resulting in highly precise and complex machined parts.
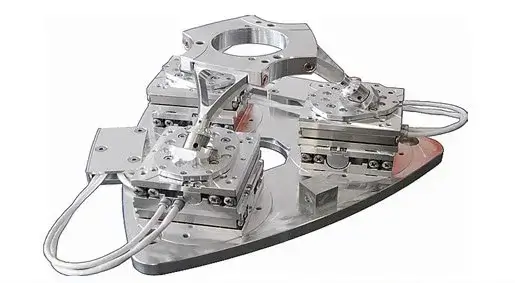
4.Precision in Motion: Axes and Their Importance
The X, Y, and Z axes in a CNC milling machine control the movement of the cutting tool and workpiece, allowing for machining with high precision and accuracy. Understanding the importance of these axes in a CNC milling machine is essential to realizing the full potential of these powerful tools.
1) The Different Axes in Milling Include:
- The Z axis controls the vertical movement of the cutting tool or workpiece, providing precise positioning and depth control during the milling process.
- The X-axis allows movement from left to right and vice versa, parallel to the cutting tool.
- The Y-axis controls the vertical movement of the part.
The combination of these three axes enables CNC machines to create complex shapes and contours in the material, resulting in precise and accurate machined parts.
2) Achieving Depth: The Role of the Z-Axis
In CNC milling, the Z-axis significantly affects the depth of cut. It regulates the vertical movement of the tool, thereby precisely controlling the depth of the machining operation. By interacting with the X-axis and Y-axis, the Z-axis is able to create complex three-dimensional parts with high precision.
Problems such as irregular Z-axis movement or inconsistent depth determination can be resolved by checking if the control card is loose or faulty, troubleshooting the coordinate determination process, or checking for jamming or slipping.
By ensuring the accuracy of the Z-axis, CNC milling machines can achieve optimal depth control, enabling the manufacture of complex and detailed parts.
3) Lateral Dynamics: Understanding the X-axis and Y-axis
The X-axis and Y-axis control the lateral movement of the cutting tool and workpiece, helping to achieve precise and uniform machining on the surface of the material. The X-axis represents the movement from left to right or right to left parallel to the cutting tool, while the Y-axis represents the movement from front to back.
Collectively, these axes determine the precise positioning and movement of the cutting tool, facilitating accurate and controlled machining on the material surface.
The CNC controller works in coordination with the motor and drive components to move the X- and Y-axes, precisely controlling the position and movement of the cutting tool during the milling process. This precise control ensures that the machined parts are consistent and meet the required specifications.
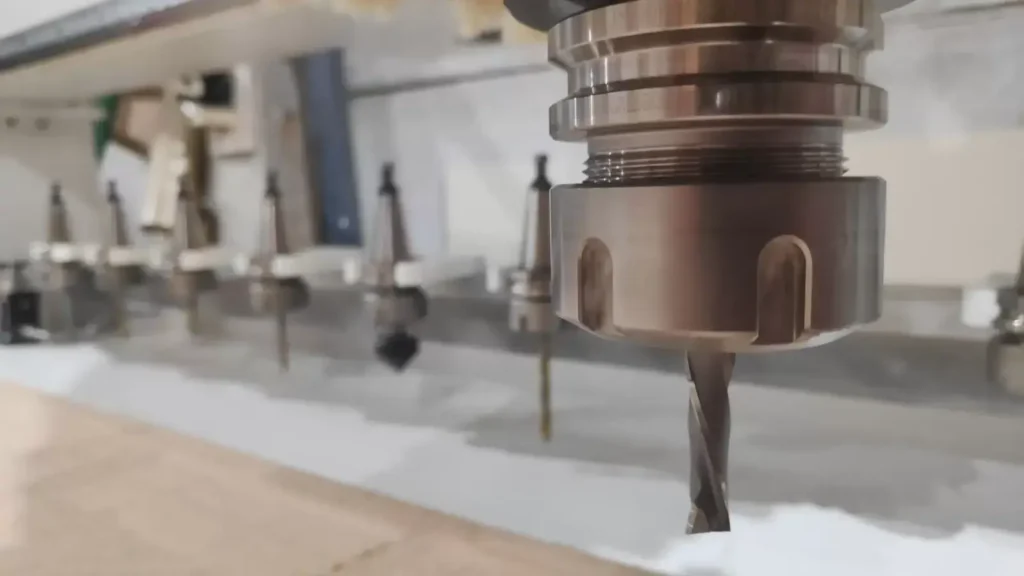
5.Cutting-Edge Technology: Tools and Accessories
CNC milling machines use a variety of machine tools and accessories, each of which plays an important role in achieving the desired machining results. From cutting tools to coolant systems, these accessories work together to increase the precision and efficiency of the machine.
Selecting the right milling tool is key to ensuring high performance and quality of machined parts. Additionally, coolant systems help extend tool life and improve surface finish, thereby reducing heat and friction during the milling process.
By understanding the role and function of these different tools and accessories, operators can optimize their CNC milling machines for maximum precision and accuracy.
1) Multi-Function Tool Changer
In CNC milling machines, tool changers enable seamless switching between different cutting tools during the milling process without stopping the machine. This feature allows multiple machining operations to be performed in a single setup, greatly improving efficiency and productivity.
There are various types of tool changers available to suit different milling operations and machining needs. These include:
- Automatic tool changer with chain tool magazine
- Turret head type
- Drum ATC
- Disc ATC
By incorporating a multi-function tool changer into the CNC milling process, operators can easily and accurately complete a variety of tasks, including using CNC routers.
2) Extend Tool Life with A Coolant System
In CNC milling, coolant systems help extend the life of cutting tools and improve the surface finish of machined parts by reducing heat and friction during machining.
By maintaining optimal cutting temperature and lubricating the cutting tool, the coolant system minimizes wear on the tool and workpiece, ultimately improving machining efficiency and extending tool life.
When choosing a CNC milling coolant, the following factors should be considered:
- Material compatibility
- Tool requirements
- Cutting conditions
- Corrosion protection
- Extended tool life
- Cost
All of these should be taken into account. By carefully selecting and using the right coolant system, operators can significantly improve the performance and life of their cutting tools and achieve a better surface finish on machined parts.
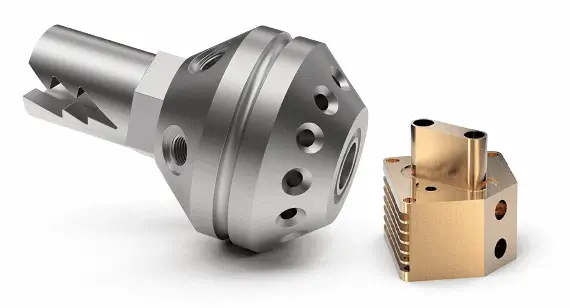
6.Supporting Roles: Minor but Essential Parts
In addition to the primary components, CNC milling machines require secondary but critical components that control the movement of the cutting tools, support the spindle, and secure the workpiece during machining.
These components, such as servo motors, ball screws, and linear guides, work in conjunction with the primary components to ensure that the machine operates effectively and efficiently.
These secondary components may not be as prominent as the core components of a CNC milling machine, but they play a vital role in achieving the precision and accuracy required for the final machined product.
By understanding the importance of these components and how they affect the overall performance of a CNC milling machine, operators can optimize their machines for maximum precision and efficiency.
1) Material Storage Area: Worktable and T-Slot
By providing a stable platform for holding workpieces during machining, worktables and T-slots ensure high precision and consistent results.
Worktables are usually made of durable materials such as aluminum or cast iron, providing a reliable surface for holding workpieces during milling.
T-slots are the components that hold and clamp workpieces, designed to work with T-nuts to firmly clamp and position workpieces during machining. T-slots offer flexibility and versatility in holding a variety of fixtures and accessories, simplifying the setup and holding of workpieces for precise milling.
Worktables and T-slots ensure precision and accuracy during CNC milling processes by providing a stable platform for materials.
2) Drive: Spindle and Servomotor
Spindle and servomotors are responsible for driving the cutting tool and controlling its movement along the axis of the machine tool, allowing for precise and efficient machining operations.
Spindle motors provide the torque, speed, and accuracy required for precise cutting and machining, while servomotors control the precise position of mechanical components by receiving electrical signals and converting them into motion.
Operators can achieve optimal performance and precision in their CNC milling machines by ensuring that the spindle and servo motors are functioning properly. These motors play a key role in driving the cutting tool and controlling its movement during the milling process, resulting in highly accurate and complex machined parts.
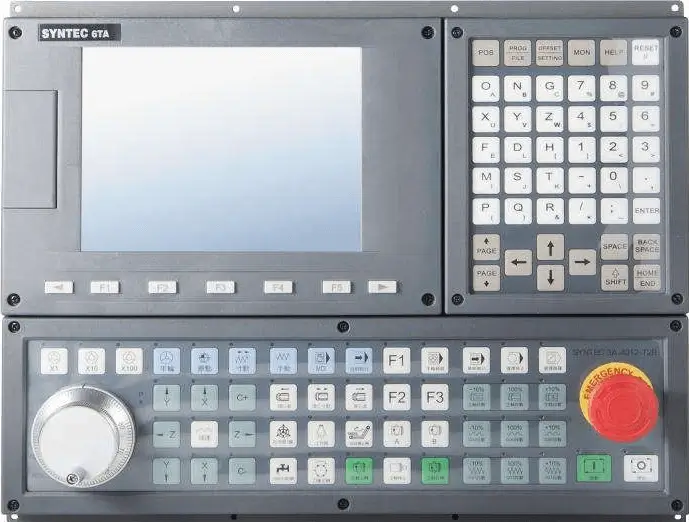
7.Improving Precision: Feedback and Control Systems
Feedback and control systems are used to improve the accuracy and precision of CNC milling machines. These systems include position feedback systems, velocity feedback systems, and adaptive control systems, which work together to verify and adjust the precise position of mechanical components during the milling process.
By incorporating these feedback and control systems into a CNC milling machine, operators can ensure that the machine maintains optimal performance and precision throughout the machining process.
These systems play a vital role in achieving the desired precision and consistency in the final machined product, making them an essential component of any CNC milling operation.
1) The Eyes of the Machine: Display Unit and Control Panel
The display unit and control panel are the primary interface between the operator and the CNC milling machine, allowing the machine’s operation to be monitored and controlled. The display unit provides the operator with important information about the machine’s status, while the control panel enables the operator to enter commands and adjust the machine’s settings and parameters.
By ensuring that the display unit and control panel are functioning and interacting properly, operators can monitor and control their CNC milling machines for optimal performance and precision.
These components play a vital role in the overall operation of the CNC milling machine, allowing the operator to achieve the desired precision and consistency in the final machined product.
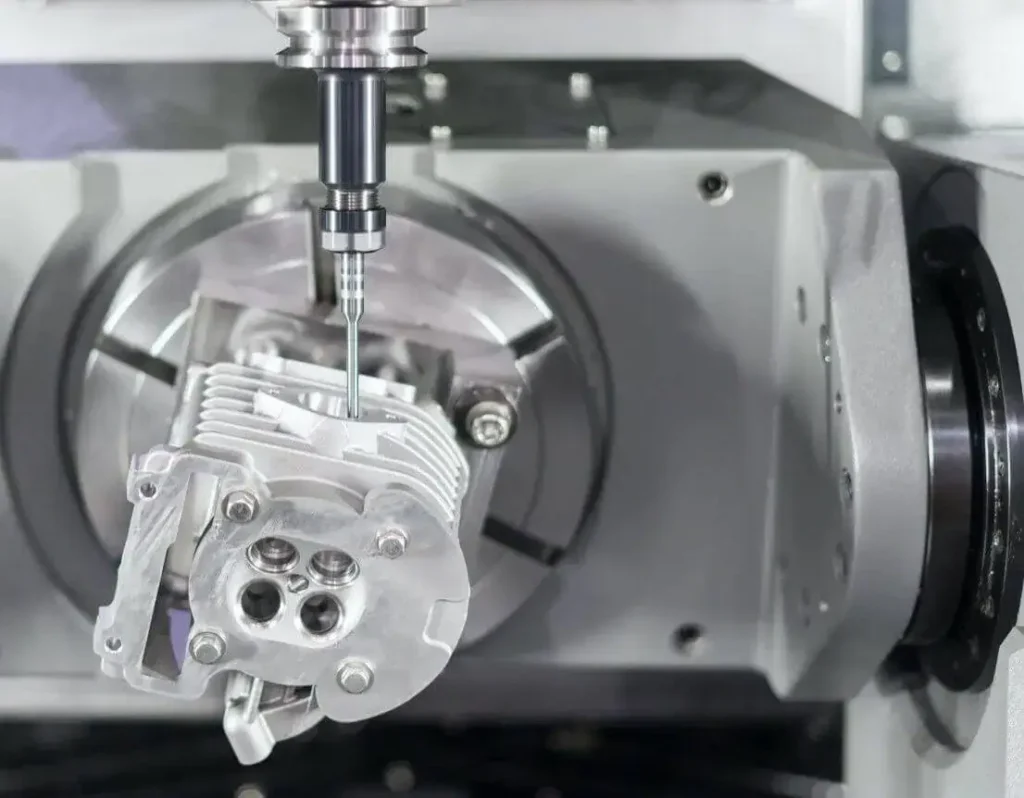
8.Customizing CNC Machining for Specific Needs
Design considerations, material selection, tool selection, and design optimization allow for customized CNC machining to meet specific needs and requirements. By tailoring the CNC machining process to meet the unique requirements of a specific project, operators can achieve precise results based on the specific needs of their customers.
A key factor in custom CNC machining is choosing between manual machining and CNC precision, taking into account the following factors:
- Accuracy
- Time
- Technical experience
- Labor
- Productivity
- Cost
By carefully considering these factors and adjusting the machining process accordingly, operators can achieve the desired level of customization and precision based on their specific needs.
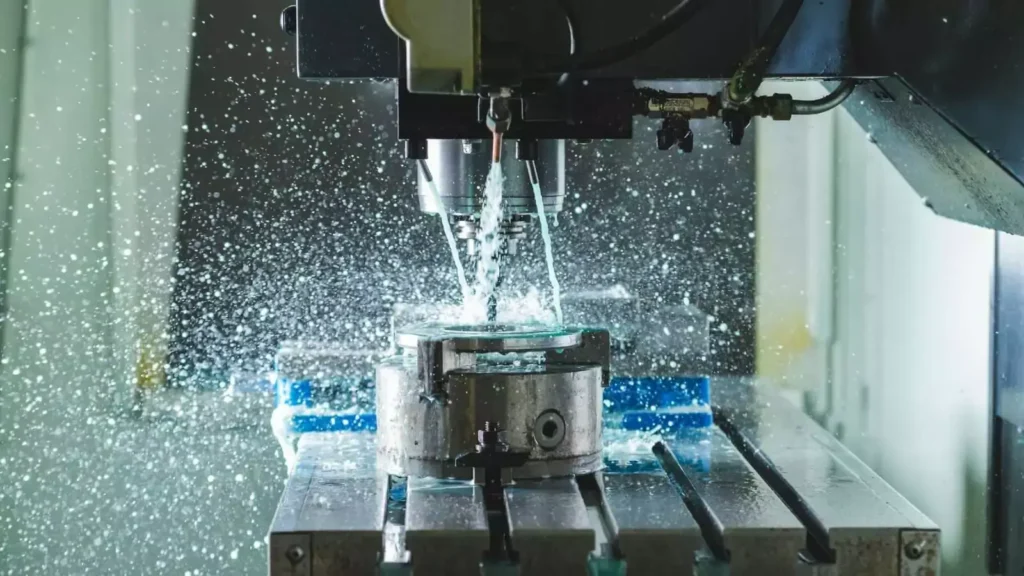
1) Adjusting Complexity: Manual Machining vs. CNC Precision
Manual machining may be suitable for simpler parts, while CNC precision is suitable for complex parts that require high accuracy and consistency.
The choice between manual and CNC precision is largely influenced by the complexity of the project. CNC machines are preferred for highly complex parts due to their ability to produce complex features such as:
- Holes
- Slots
- Grooves
- Pockets
These features can be created on any surface of the workpiece. In contrast, manual machining offers flexibility and adaptability for unique or complex part geometries, making it a viable option for certain projects.
By understanding the unique requirements of each project and adjusting the machining process accordingly, operators can achieve the best level of customization and precision for their specific needs.
9.The CNC Milling Process
We can break this process down into three phases:
Stage 1: Create a 2D or 3D CAD Model
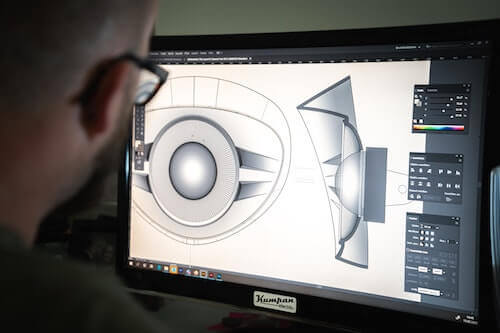
The first step in the CNC milling process is to create a 3D (or 2D) drawing of the desired part using CAD/CAM software such as Autodesk Inventor, Fusion 360, and SolidWorks. These computer-aided design (CAD) or computer-aided manufacturing (CAM) tools allow you to specify dimensional and tolerance requirements.
Stage 2: Convert the CAD Model to a CNC Program
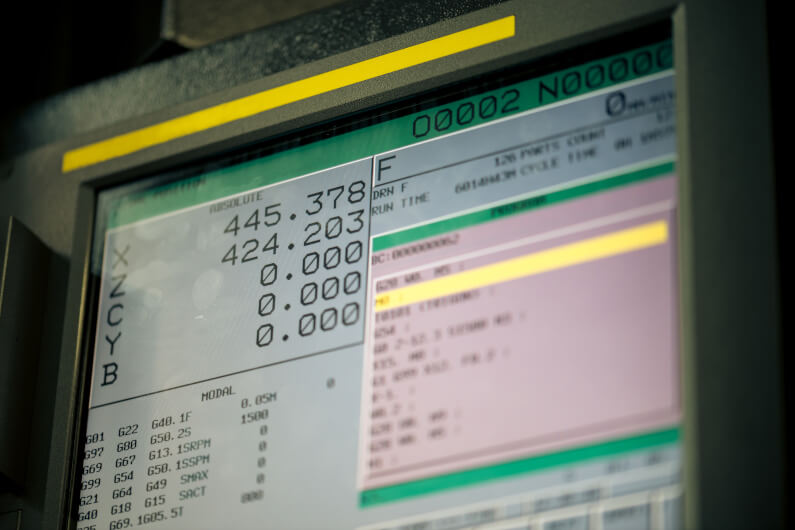
Export your CAD model to a CNC-compatible file using the CAM software we mentioned in Phase 1. CAM tools have features that allow you to convert 3D CAD models into a computer program called G-code.
The G-code will then automatically perform all the operations required to manufacture the part, such as the cutting sequence, tool paths, machine speeds, workpiece movement, and more.
Stage 3: Set up the CNC Mill and Perform the Milling Operation
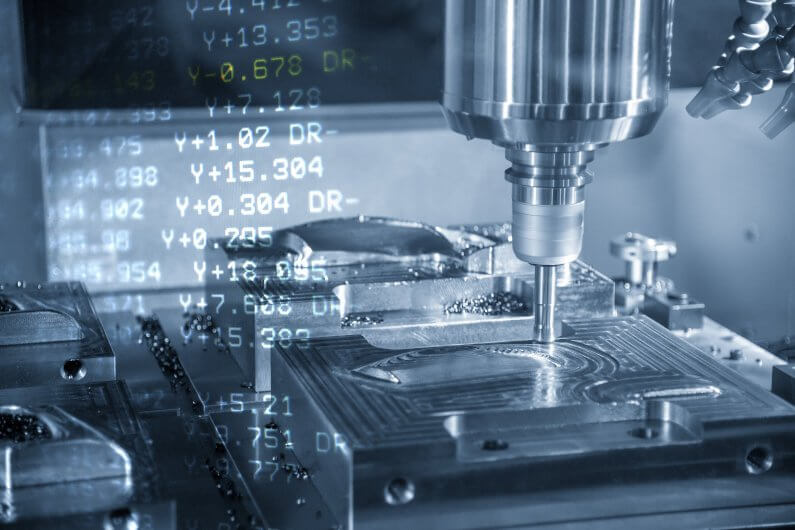
In this stage, you will insert the workpiece into the CNC machine work surface, mount the cutting tool to the CNC machine’s spindle, and download the G-code you created in Stage 2.
Once all of these steps are complete, proceed to launch the machining program. The milling machine will perform all the operations required to turn the workpiece into the desired part.
10.3 Common CNC Milling Operations
Here are a few of the most commonly used milling operations today:
1) Face Milling
Face milling is arguably the most common type of milling operation used to create flat surfaces. This machining operation places the axis of rotation of the cutting tool perpendicular to the surface of the workpiece being machined.
As the name suggests, face milling operations involve the use of face milling cutters. These cutters have multiple, interchangeable tool inserts that allow you to efficiently produce the desired surface in one go.
Face milling can also help you achieve a higher quality surface finish than perimeter milling. This is because the design of face milling cutters allows you to tightly control the machining operation, allowing you to remove less material than with peripheral milling.
2) General Milling
Face milling, also known as slab milling, is a milling operation used to machine flat horizontal surfaces. During the machining operation, the axis of the cutting tool is parallel to the surface being machined.
The process uses a special type of tool with teeth located at the periphery to facilitate the machinist to perform the cutting operation.
3) Angular Milling
Like face milling, angular milling also helps you create flat surfaces. The two operations differ only in the way the cutting tool is set up.
In angular milling, the axis of the cutting tool is at an angle to the surface of the workpiece. This allows features such as grooves, serrations, and chamfers to be created.
11.Some Advantages of CNC Milling
- CNC milling machines have higher accuracy and precision than many modern manufacturing technologies.
- Multi-axis CNC machines can create extremely complex geometries while meeting tight tolerances as tight as +/-0.004 mm.
- CNC machines are compatible with a wide range of materials, including plastics, composites, and metals.
12.Material Considerations in CNC Milling
Materials used in CNC milling are generally classified into three main categories: plastics, soft metals, and hard metals. Some examples of materials include aluminum, bronze, copper, ceramics, plywood, steel, stone, wood, and zinc.
1) Metals

Both soft and hard metals can be used in CNC milling. Soft metals such as aluminum and bronze are well suited for CNC milling because they are brittle and corrosion resistant. They are often used to produce aircraft parts, building materials, medical components, gears, shafts, and more.
Hard metals such as steel and stainless steel are popular alternatives to aluminum in CNC machining. This is due to their strength and resistance to high temperatures, so they are relatively easy to machine.
2) Plastics
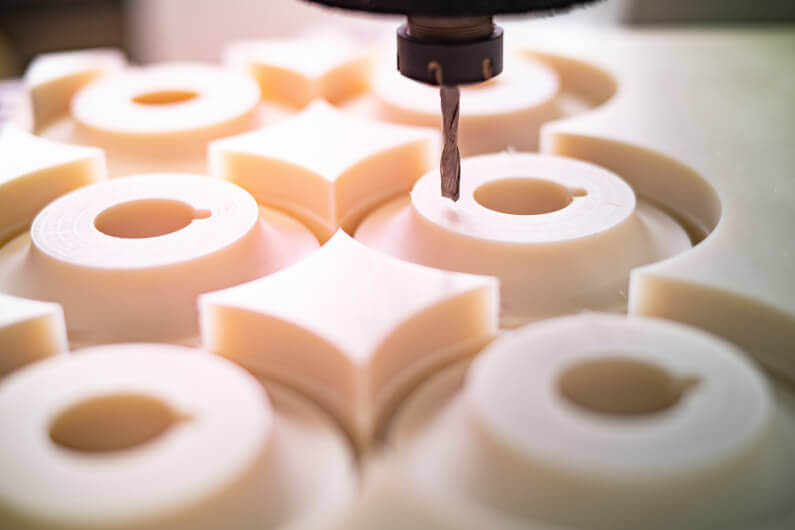
Plastics are another common material used in CNC milling. They are lightweight, corrosion resistant, and can be molded into complex shapes. They are often used in industries such as automotive, medical, and consumer products.
3) Ceramics
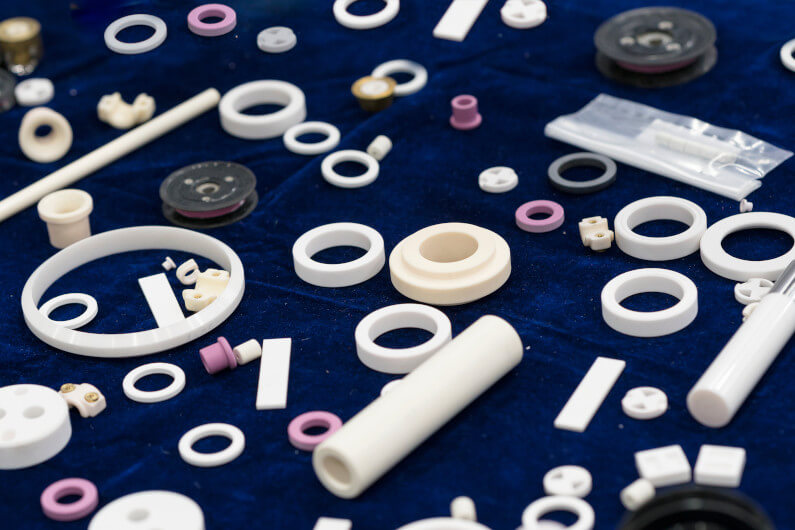
Ceramics are used in CNC milling because of their hardness, heat resistance, and electrical insulation. They are commonly used in industries such as aerospace, automotive, and medical.
4) Wood and Plywood
Wood and plywood are used in CNC milling because they are easy to cut and shape. They are often used in industries such as furniture manufacturing and construction.
5) Glass
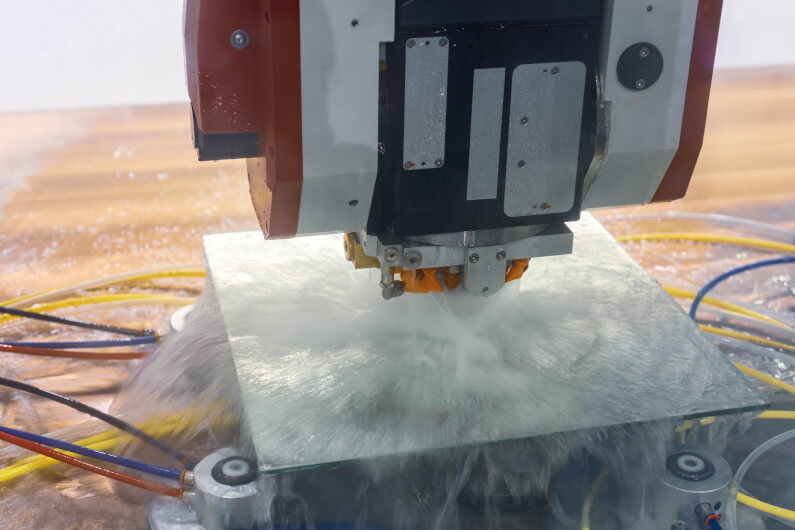
Glass is used in CNC milling because of its transparency, heat resistance, and electrical insulation. It is often used in industries such as electronics, automotive, and medical.
6) Composites
Composites are used in CNC milling because of their strength, light weight, and corrosion resistance. They are often used in industries such as aerospace, automotive, and marine.
7)Choosing the Right Material for Your Project
When choosing a material for a milling application, several factors should be considered. These factors include the material’s machinability, the properties required in the final product, production volume, and material cost.
For example, if high production volumes are required, a material that is easy to machine and relatively inexpensive would be an ideal choice. On the other hand, if the final product needs to have high strength and corrosion resistance, hard metals or composites may be the best choice.
13.CNC Milling Applications
CNC milling is one of the most precise manufacturing technologies and is ideal for creating complex designs. Its applications are wide-ranging, covering a variety of industries and products. Here are some common uses for CNC milling:
1) Aerospace Components
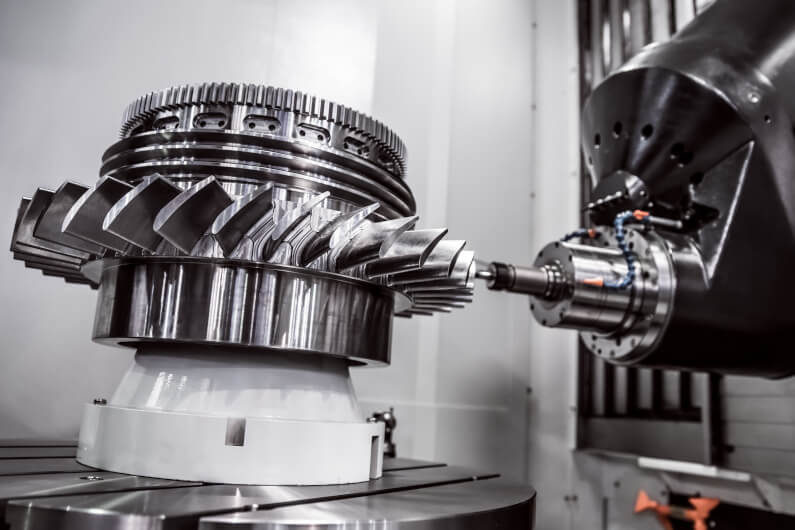
The aerospace industry requires parts that are both lightweight and durable. CNC milling is used to create complex parts that can withstand the harsh conditions of space travel. These parts include engine parts, structural parts, and other complex parts.
2) Medical Components
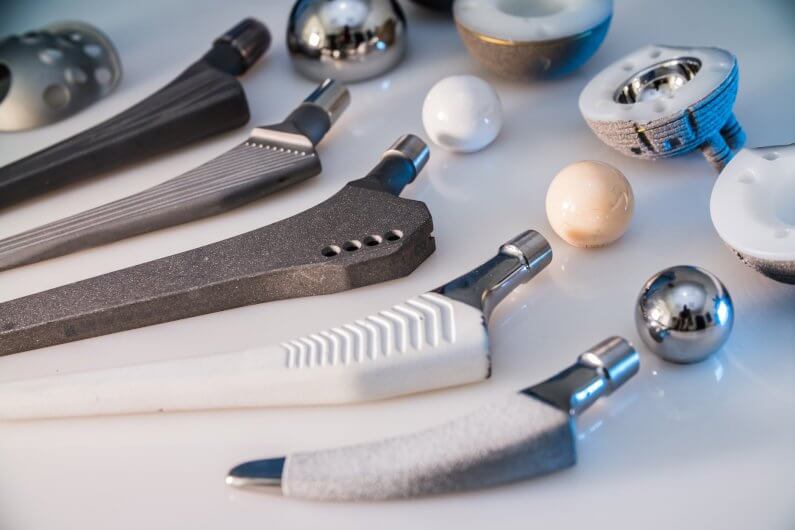
The medical industry requires precise and reliable parts. CNC milling is used to manufacture medical devices and components, such as surgical instruments, implants, and medical machinery parts.
3) Robotics
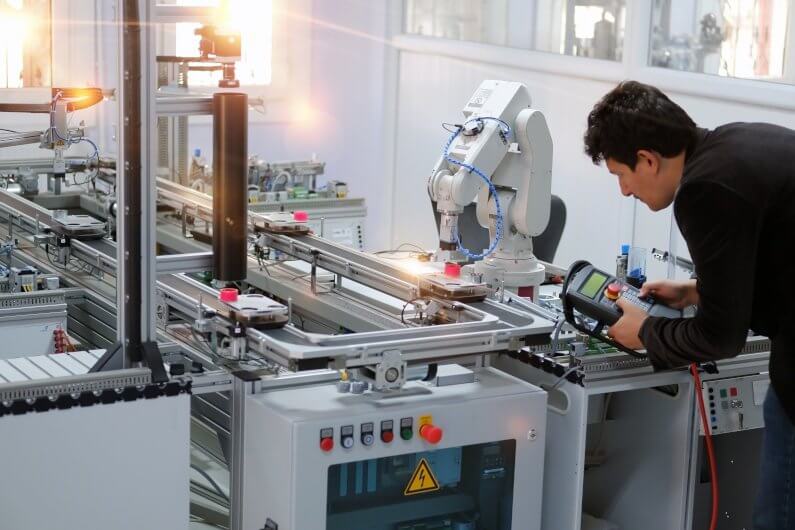
In the field of robotics, CNC milling is used to manufacture the precise and complex parts required for robots. This includes everything from structural parts to complex gears and mechanisms.
4) Automotive
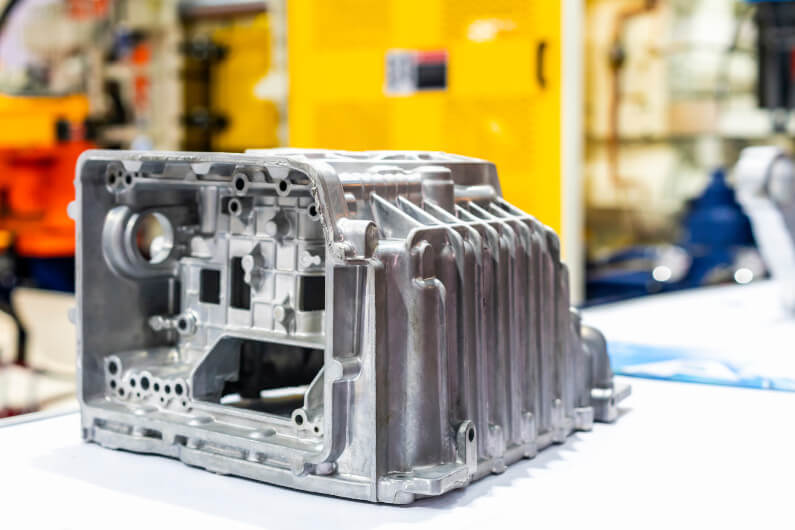
In the automotive industry, CNC milling is used to manufacture vehicle parts. This includes everything from engine parts to body parts.
CNC milling is a versatile manufacturing technology that is used to manufacture a wide range of products across many industries. Its ability to create precise and complex parts makes it a popular choice for many manufacturers.
14.Design for Manufacturability with CNC Milling
Design for Manufacturability (DFM) with CNC milling involves creating designs that are easy to produce and cost-effective. This includes considering part size, standardization, and material selection.
1) Part Size
The size of a part can significantly impact the cost and feasibility of CNC milling. Larger parts require more material and time to machine, which increases costs.
On the other hand, very small parts can be difficult to machine accurately. Therefore, it is critical to design parts that fit the capabilities of a CNC milling machine.
2) Standardization
Standardization can also reduce the cost of CNC milling. This involves designing parts that can be manufactured using standard tool sizes and avoiding complex features that require specialized tools.
For example, adding internal corner radii to parts, avoiding thin walls and sections of parts, and choosing larger features over smaller ones can all help reduce the cost and complexity of the milling process.
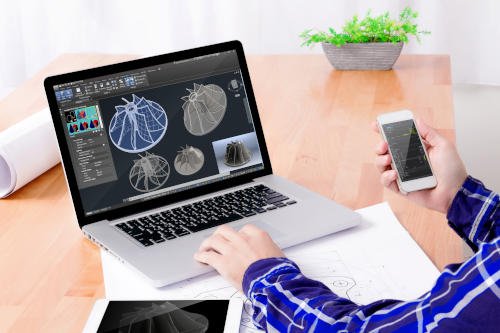
15.Frequently Asked Questions
1) What are the 7 main components of a milling machine?
A milling machine consists of seven main components: column, knee, saddle, table, ram, headstock, and their associated components.
2) Why is CNC milling so expensive?
CNC milling machines are expensive due to their complex components, high maintenance costs, and precision engineering. The complexity of the machine increases the cost, as does the level of capability required. As a result, industrial CNC milling machines can be expensive to operate.
3) How do the X, Y, and Z axes affect the accuracy of a CNC milling machine?
The X, Y, and Z axes of a CNC milling machine are critical to its accuracy because they control the movement of the cutting tool and the workpiece, allowing for precise, accurate machining.
4) What role do tools and accessories play in CNC milling?
Tools and accessories are essential to CNC milling because they increase the precision and efficiency of the machine, ensuring accurate machining results.
5) How can CNC machining be customized to meet specific requirements?
CNC machining can be customized to meet specific requirements by considering design, material selection, tool selection, and design optimization.
16.Conclusion
There is no doubt that CNC machines can accurately manufacture complex geometries and meet tight tolerances. But like other machining technologies, the success of a CNC milling project depends primarily on the CNC milling machine operators, technicians, and engineers. That is why it is imperative that you find the right manufacturer for your project.